Next Meeting
Wednesday April 17, 7 pm
Bridges Church,
625 Magdalena Ave,
Los Altos 94024

Program
Rose Engine/Ornamental turning live demo with Brad Bond
President’s challenge:
Turn a lidded bowl or canister.
Upcoming Meetings
- May: Spindles, one, two, too many!
- June: ?
Upcoming Demos
- Sally Ault – June 9 10:00-4:00 at MakerNexus Sunnyvale, $30.00 at the door.
- Eric Lofstrom – October, details to follow
Last Meeting Review, March 20, 2024
Notes by Laura Rhodes, pictures by Angela Gunn and Roman Chernikov
Announcements
- There were 46 attendees for the Mike Mahoney demo.
- Sally Ault will be demonstrating for our clubs on June 9 at Maker Nexus. Signups are available online (NEED LINK HERE).
- Laura Rhodes spoke about the opportunity to exhibit wood creations at the Bay Area Woodworkers Association (BAWA) Fine Woodworking Show on June 8 and 9. More information is available on the BAWA website, https://www.bayareawoodworkers.org/Shows/Show2024/ShowPage_2024.html
- Only a limited time is left for the sign up for the AAW Symposium at a discounted price.
- Jerry Galli promoted turning pens for the troops. Currently he is out of kits, but he expects more to come soon. Contact Jerry if you would like pen kits to turn for this effort.
- Jon Bishop reminded members that annual WBW dues will go up to $45 if not paid before the end of March.
Finishing Part 2 – Finish types and application
This was the second part of a two-part series of discussions on how to get a museum quality finish on your turned pieces. Panel on finishing. Left to right: Dennis Lillis, David Vannier, Jon Bishop, Robert Bley.

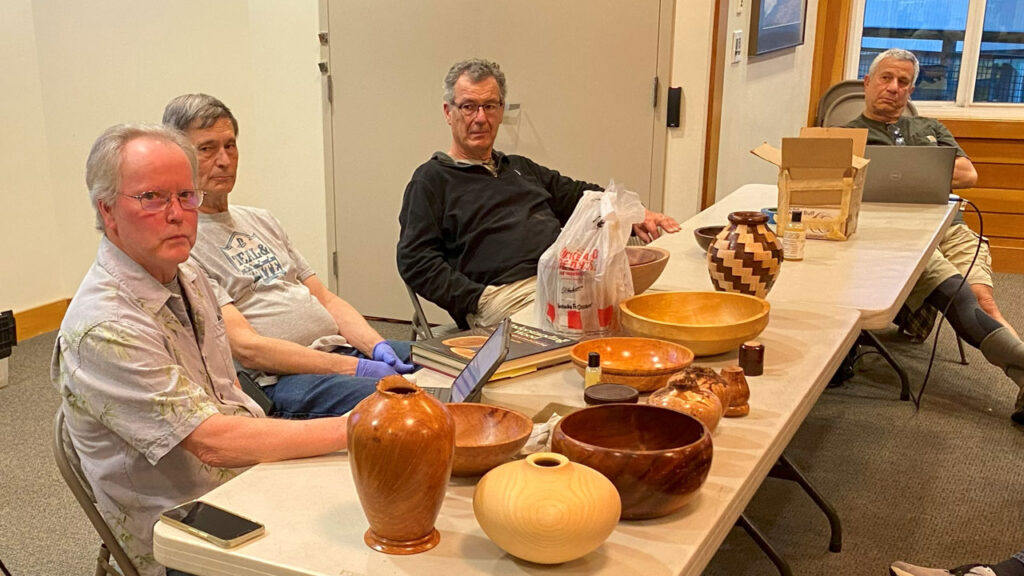
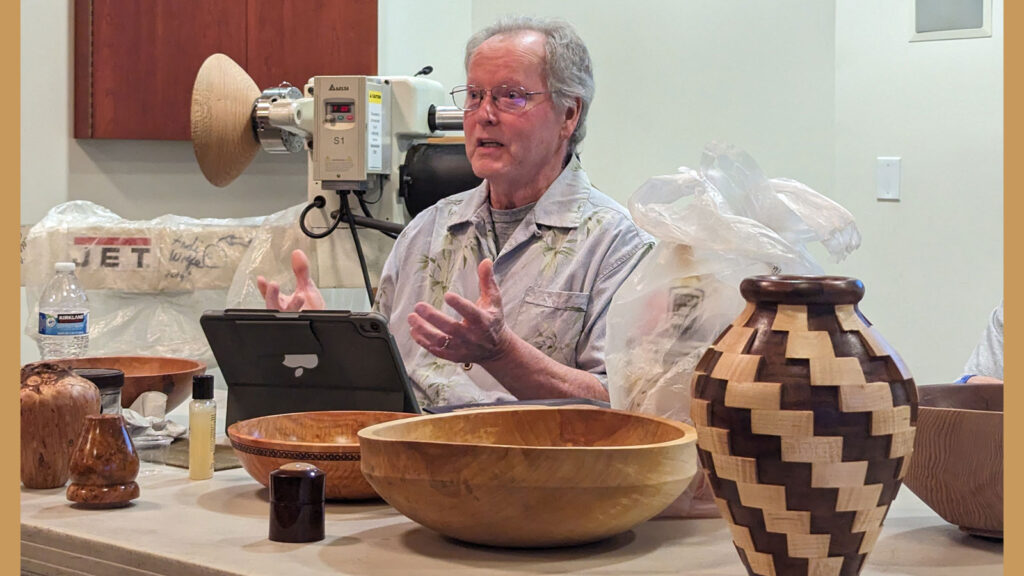
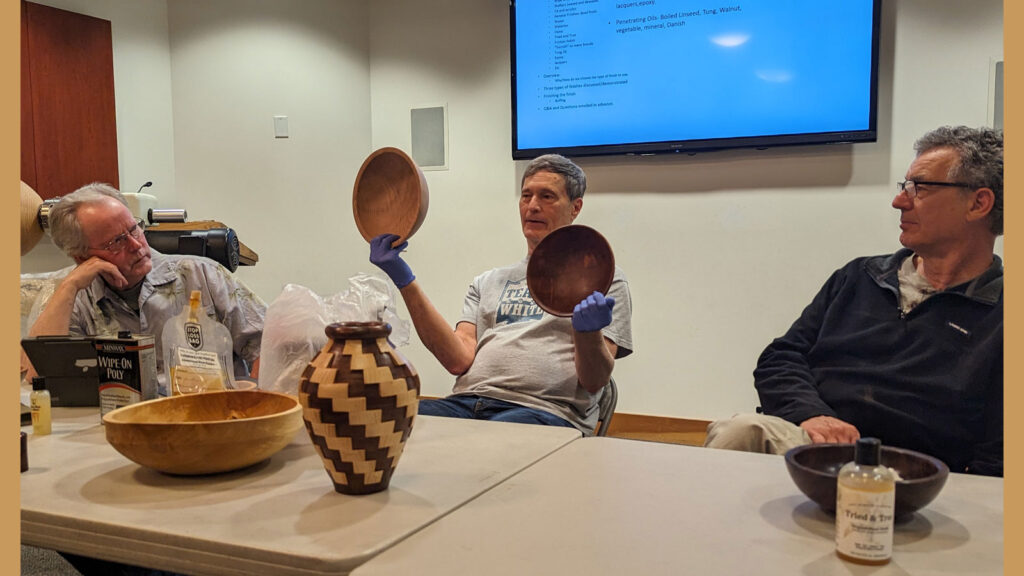
Bob spoke a bit about safety. Most of the wood finishing products have some level of toxicity. Be sure to wear gloves and a respirator and work in a well-ventilated area. Beware of spontaneous combustion of oil soaked rags. Dry them flat on a non-flammable surface. When stiff, they are safe to discard.
Dennis Lillis described the purpose of finish and some of the different kinds of finish:
- Level of shine might be a selling feature.
- Varnishes offer a high degree of protection but may be hard to apply
- Water-based polyurethane doesn’t yellow as much as oil-based.
- Shellac was recommended as a sanding sealer because it is compatible with other finishes that may be applied on top of it. Make sure to use the de-waxed kind. Bob prefers to make his own shellac using the blond flakes and alcohol to prevent changing the color of the wood.
- Finishes (such as Spar Varnish) with UV inhibitors are not food safe.
- Wax only as a finish looks great initially but is only good for items that will only sit on the shelf. With handling, the item will lose its appeal within a short time.
- CA glue as a finish is good for small objects.
- Howards Butcher Block Conditioner which is a mix of food-grade mineral oil, beeswax and carnauba wax may be good for those allergic to other finishes.
Two books were highly recommended:
- Understanding Wood, A Craftsman’s Guide to Wood Technology by Bruce Hoadley
- Understanding Wood Finishing by Bob Flexner
- Foolproof Wood Finishing by Teri Masachi
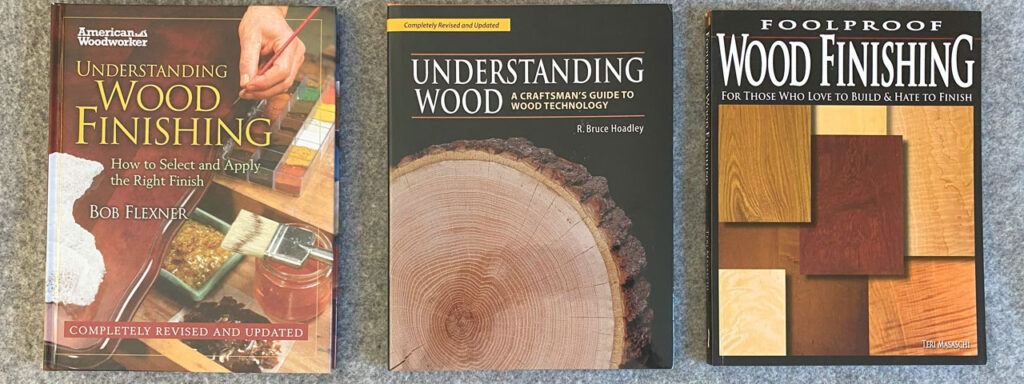
Dennis demonstrated how he applies a Wipe On Poly finish. Dennis prefers to use the oil-based MinWax Wipe on Poly, gloss version. There was a lively discussion about whether the new MinWax packaging labeled “Warm Gloss” is the same as the old “Clear Gloss” versions. Note that Dennis, Dave, and Jon do not like the Watco wipe on poly product. Dennis uses Mirka Mirlon abrasive pads instead of steel wool. To get rid of nibs embedded in a layer of the finish, he uses Abralong foam backed sandpaper 500 or 1000 grit.
Dennis places a small amount of finish in a small cup and thins it down with mineral spirits. He uses a small piece of clean T-shirt material to apply the finish to the bowl while the bowl is turning on the lathe. Immediately after application, he wipes off the excel with a clean cloth. After the layer has dried (usually a couple of hours), he will apply the next coat in the same way. Multiple coats may be required, depending on the wood, temperature, humidity.
Dave Vannier demonstrated how he applies General Finishes Wood Bowl Finish (formerly known as “Salad Bowl Finish”). He finishes on the. He folds over a paper towel (so that no rough edges are exposed), pours finish onto the towel, and applies the finish to the bowl with the lathe off. After application, he turns on the lathe and burnishes using the same application towel. Dave waits 24 hours between coats and does sand between coats. He keeps the Wood Bowl Finish in a StopLoss bag to prevent oxidation.

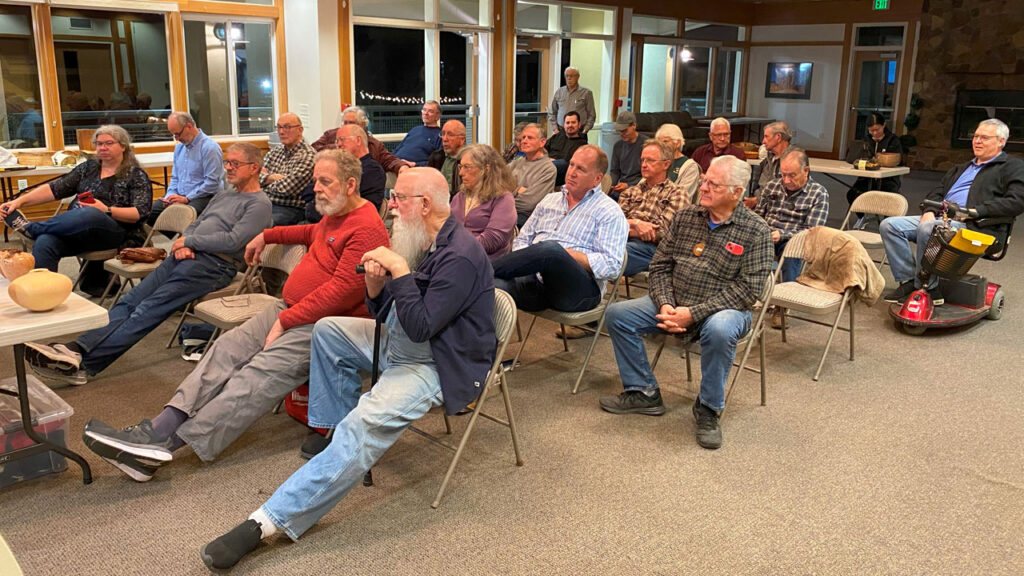
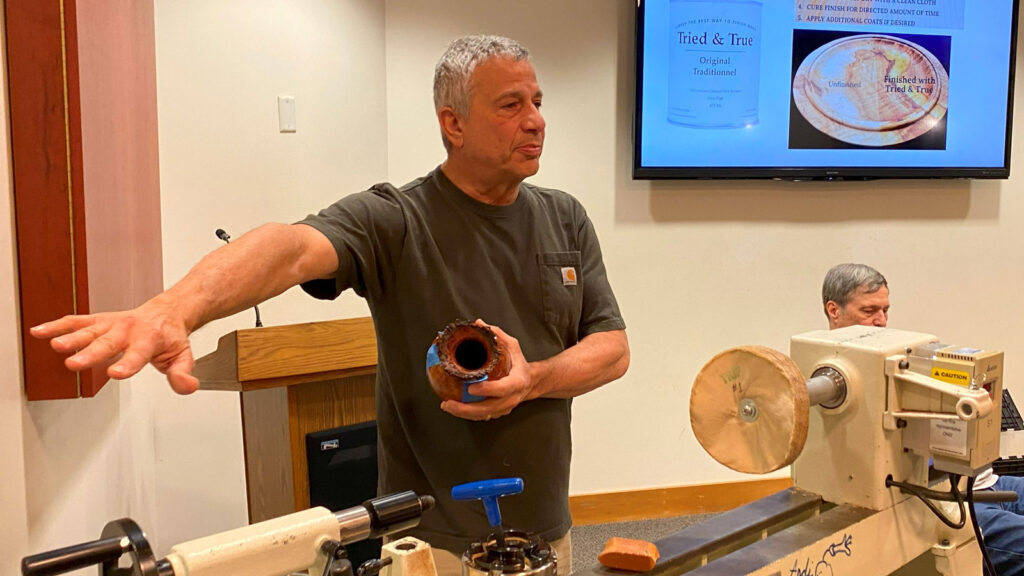
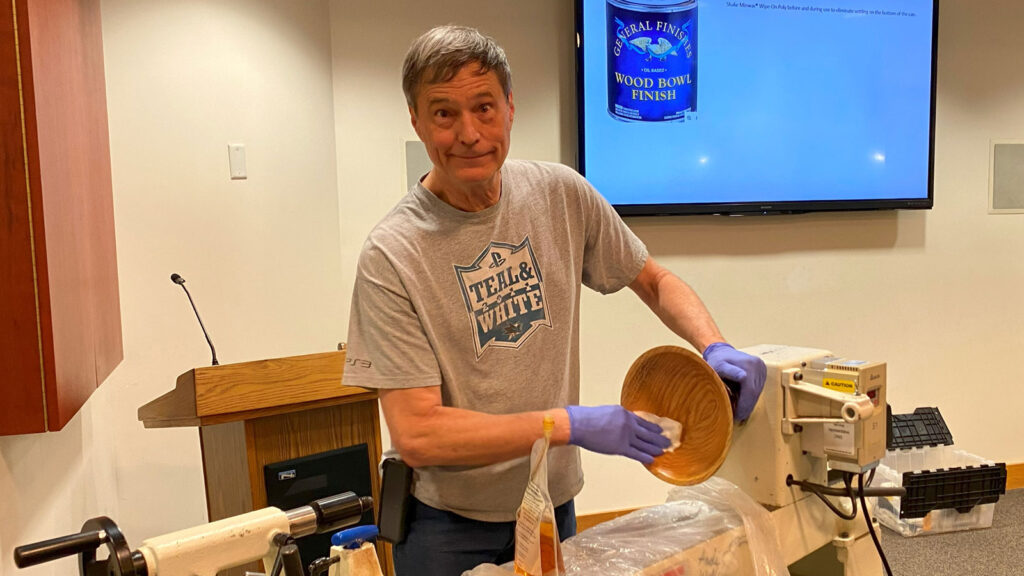
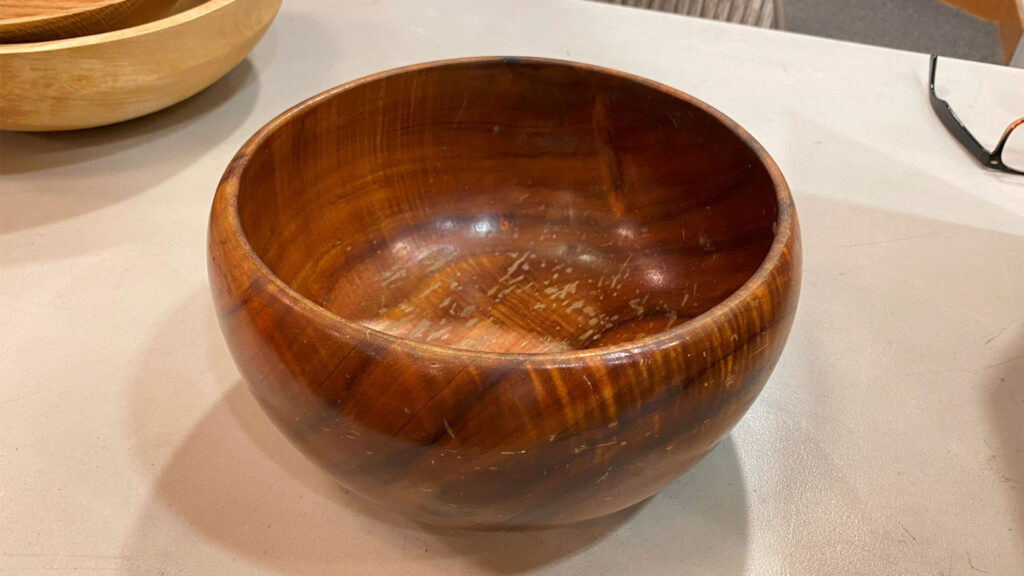
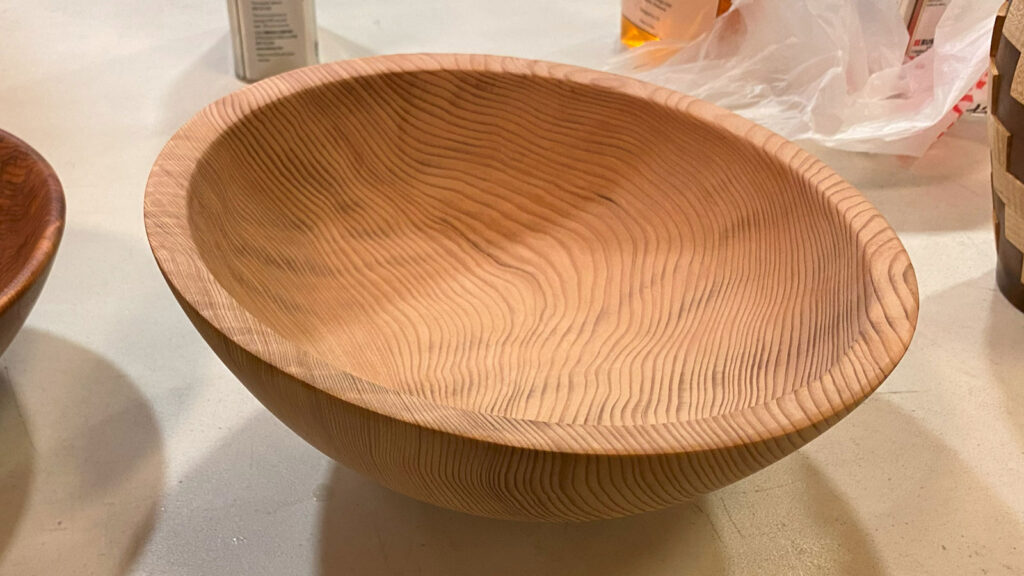
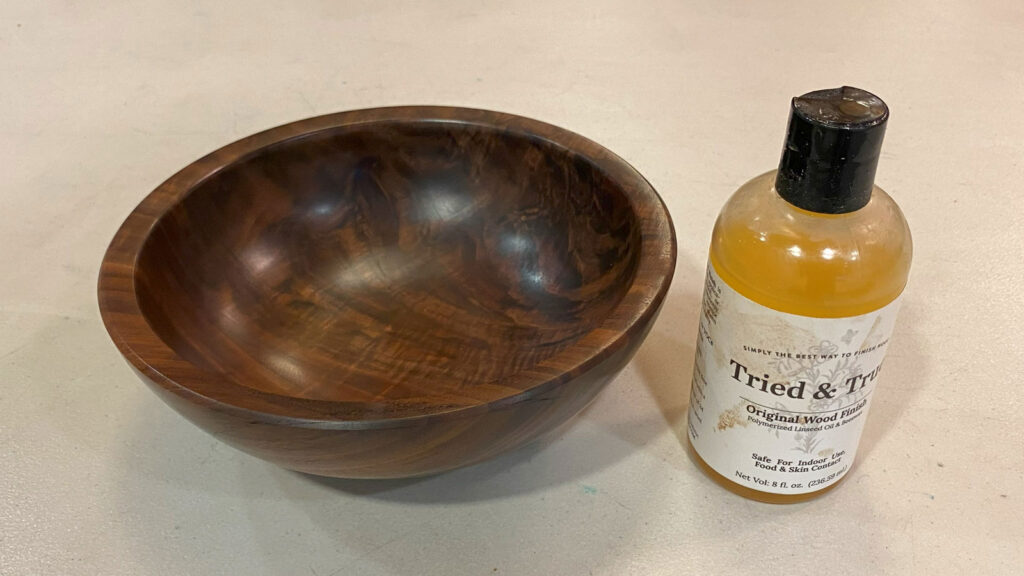
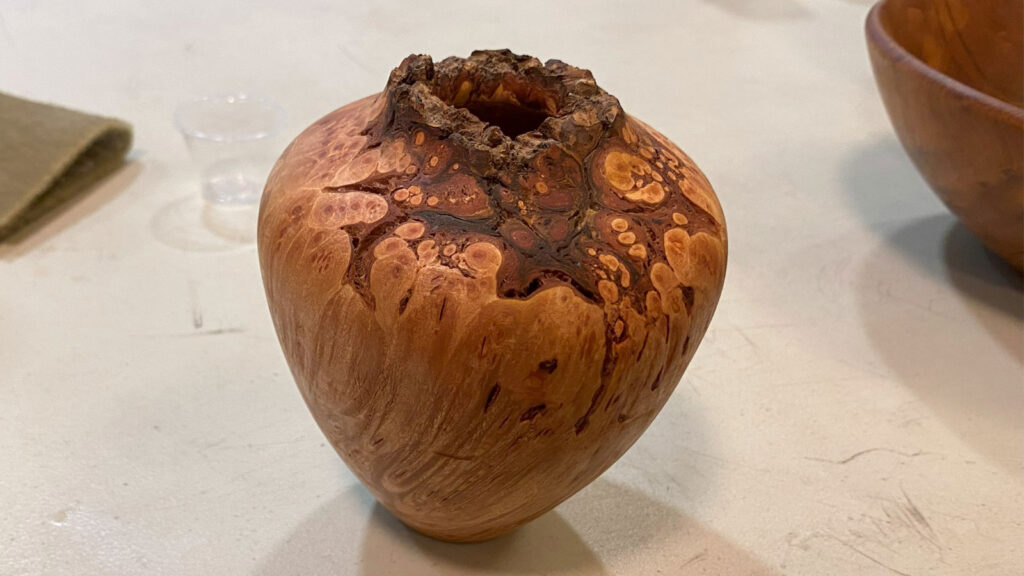
Jon spoke about applying his current favorite finish – Tried & True Original Wood Finish which is a polymerized linseed oil and beeswax. This finish is advertised as being safe for indoor use, food, and skin contact. He applies this coat, waits an hour and then wipes it all off. After 24 hours, he burnishes on the lathe using steel wool before applying a second coat.
Bob demonstrated burnishing using the Beall Buffing System. This system consists of a mandrel and three burnishing wheels and three different buffing compounds. Bob stressed the importance of avoiding contamination between the different wheels and compounds. The first compound is Tripoli which is approximately 1500 grit. The next is white diamond (~3000 grit). Finally there is Carnauba wax. Bob talked about taking care when using the buffing wheel to avoid inadvertently launching the object being buffed.
Presidents Challenge – Turn a Thin-walled bowl a la Mike Mahoney:
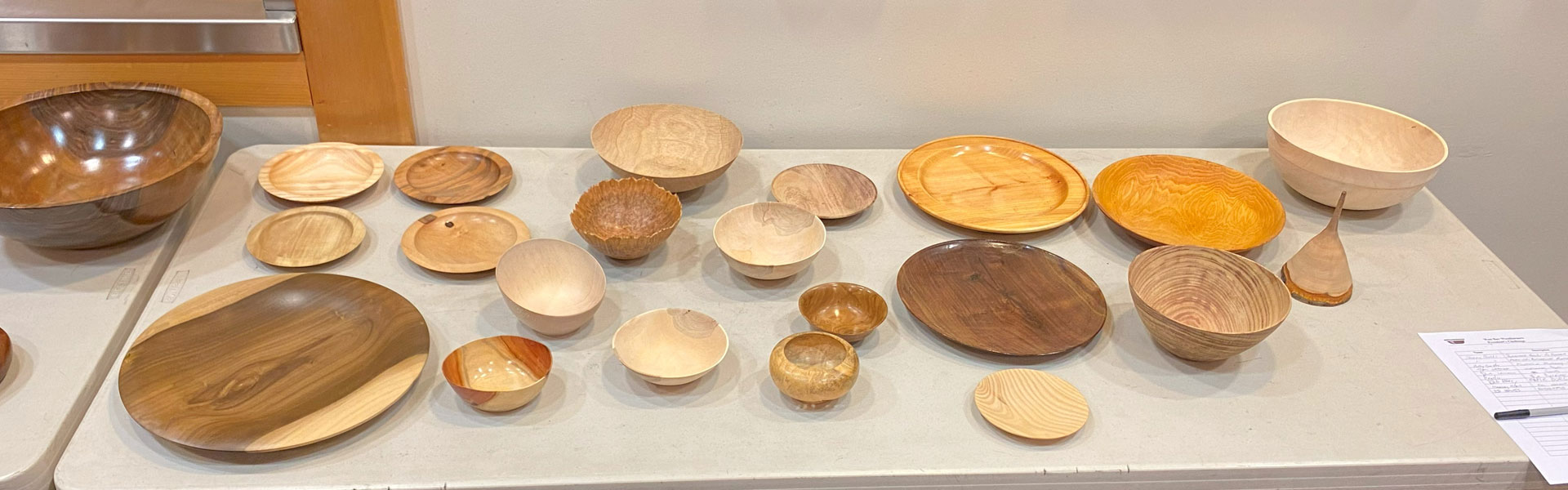
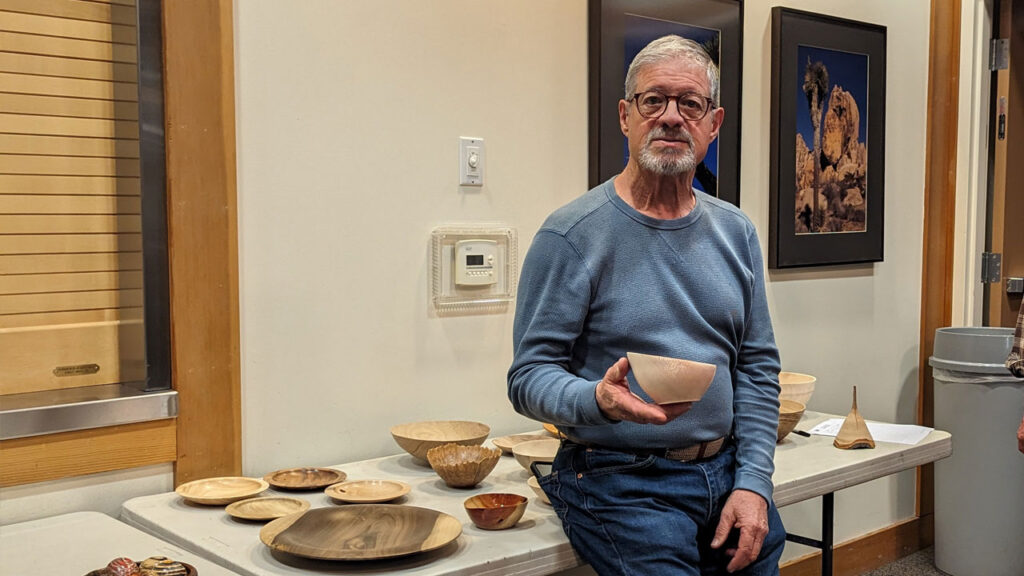
Jerry Galli – showed a sycamore bowl with no finish. Since he didn’t show it at last month’s President’s Challenge, he also presented a butternut platter finished with Ack’s paste and Doctor’s Walnut Oil.
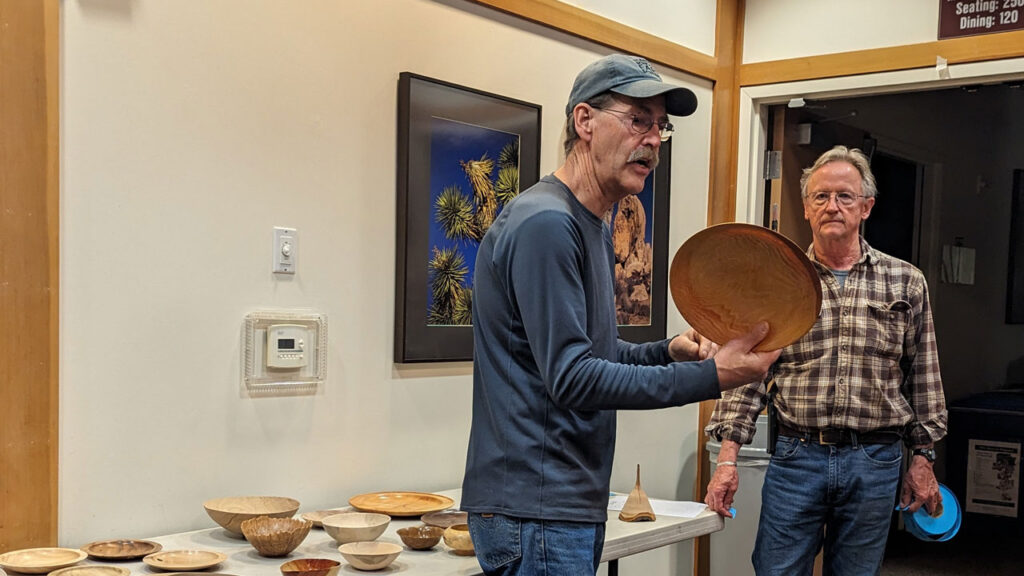
Kelly Smith – brought a very thin cedar plate. He also brought Mike Mahoney’s thin-walled bowl which Kelly won in the raffle. He noted how the bowl started making “sizzling sounds” on the way home from the demo.
Huge thanks to Kelly for bringing and donating a track load of freshly cut madrone and live oak and sharing the wood with the club members. Kelly cut the wood nicely and even finished the ends with Anchorseal. Thank you, Kelly, much appreciated!
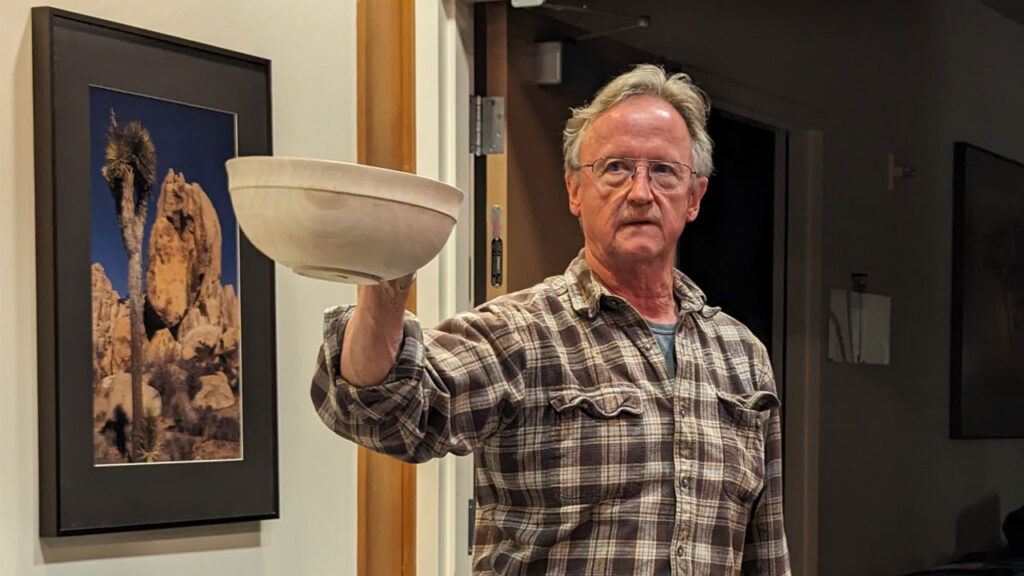
Tom Gaston – made a podocarpus thin-walled bowl in the style of Mike Mahoney with a slightly thicker rim band for stability. He noted that the bowl was still wet and still moving.
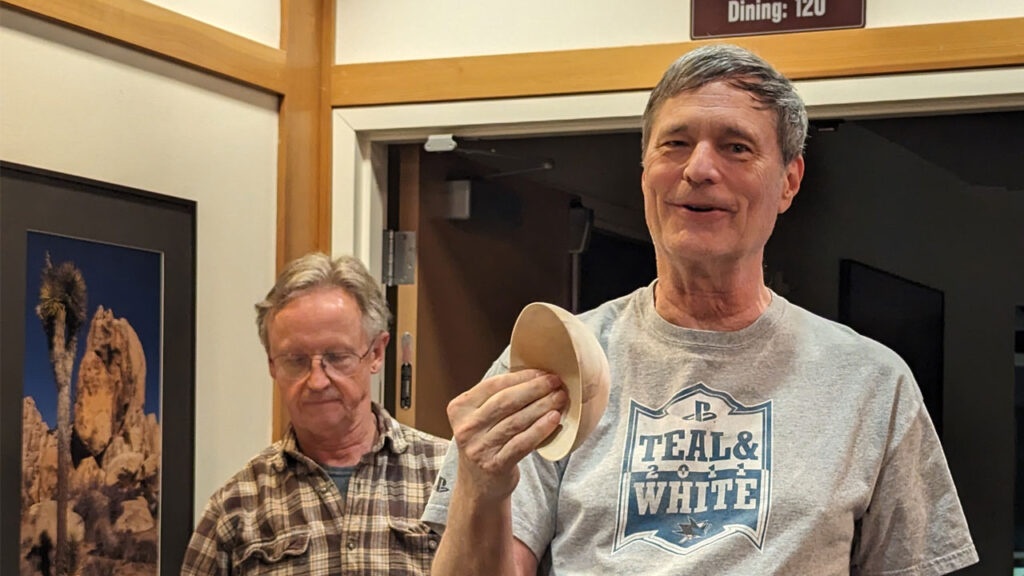
Dave Vannier – showed a black acacia plate that was a little too thin. He also turned two birch tin-walled bowls that he plans to pierce. Stay tuned for the results.
Visit Dave’s website www.daves-turned-art.com.
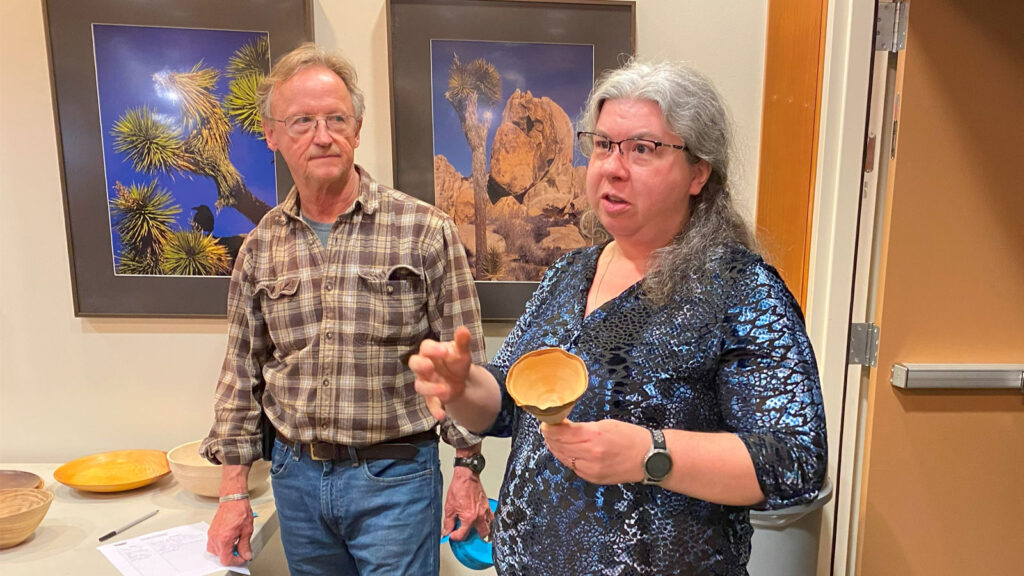
Angela Gunn – brought a loquat thin-walled flower. She noted how the wood was initially white, then turned pink and finally yellow. It has no finish.
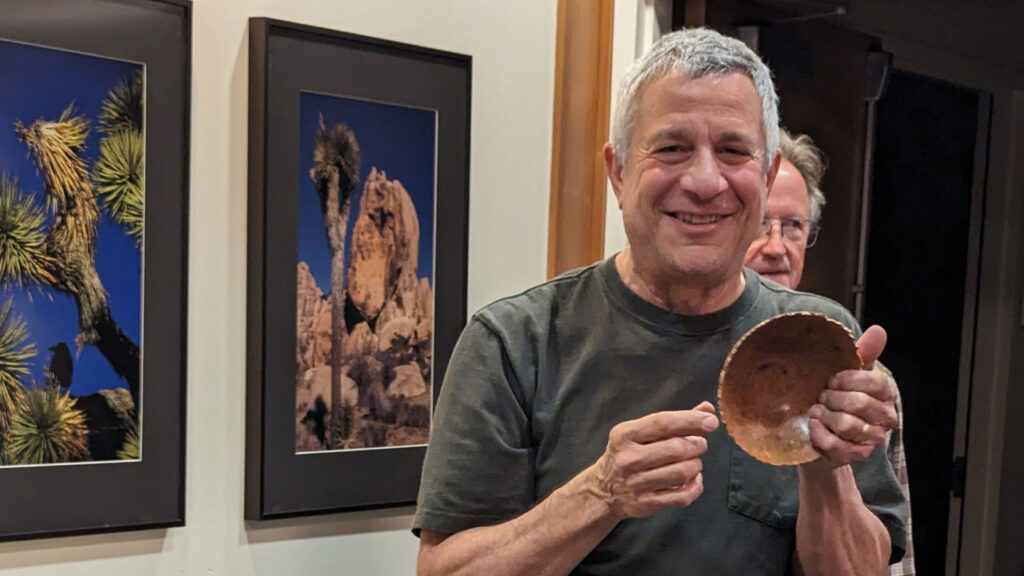
Bob Bley – showed two thin pieces. One of buckeye burl, the other, maple burl with a natural edge. He noted that the maple piece’s rim is thinner than the rest, making the illusion the bowl is thinner elsewhere.
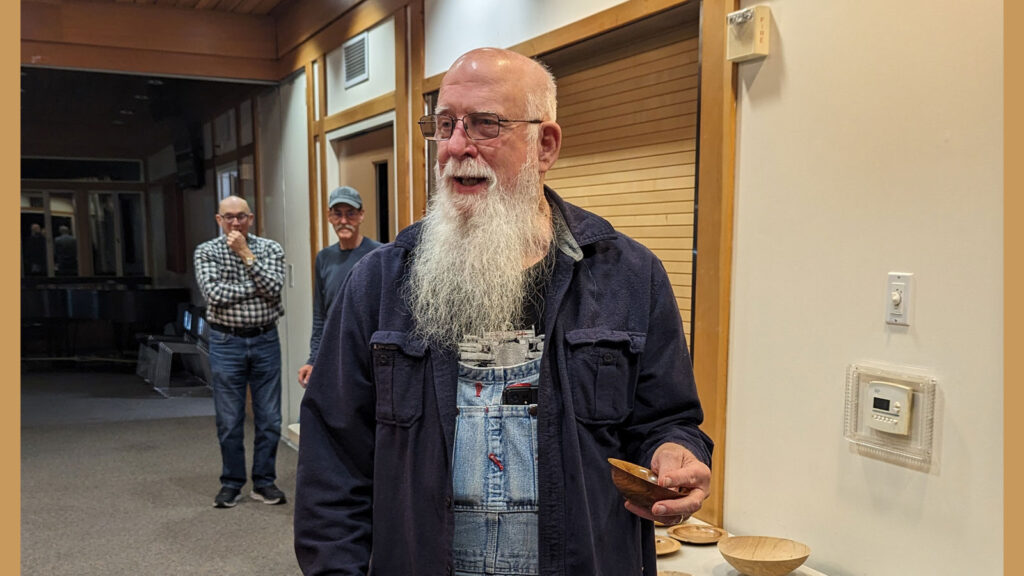
Harvey Klein – brought an ash plate and a small bowl of “mystery wood”. Harvey also told a story of inadvertently making a “donut” during a thin bowl competition years ago and how the donut became immortalized on a plaque.
Show & Tell:

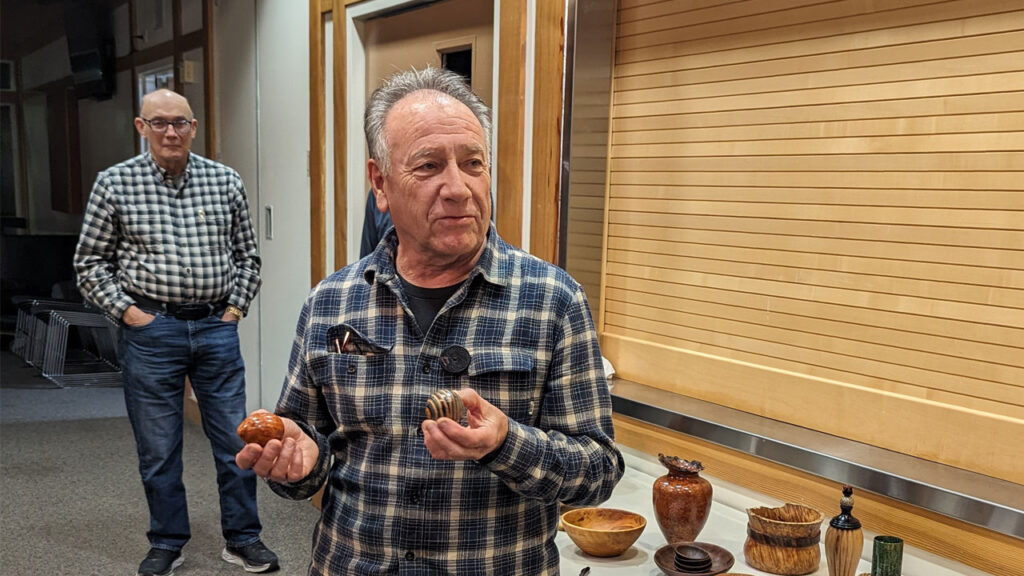
Jon Sauer – was tasked with making two dozen wooden eggs for a family party. He brought several of them to show to us. Made of a variety of exotic woods, Jon finished them with a CA finish, sanded to 2000 grit (using a sponge-backed sandpaper) and then applied lacquer.
Visit Jon’s website: https://www.jonsauer.com/
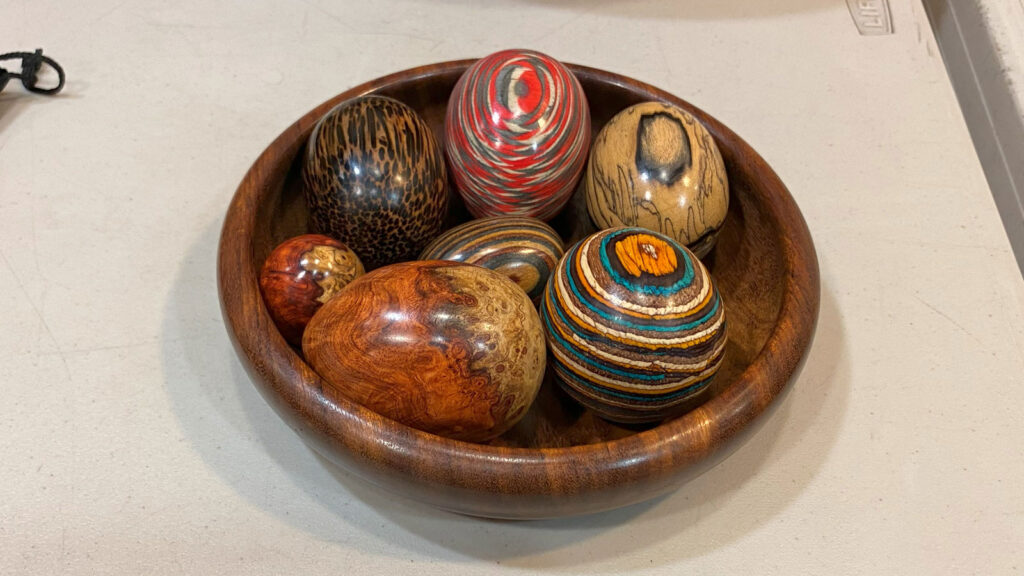
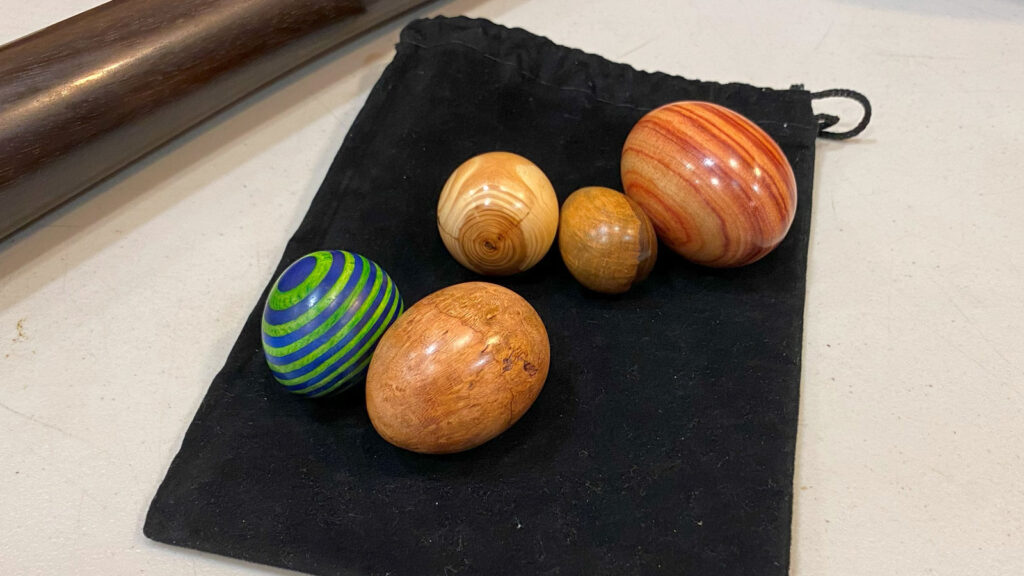
Jerry Galli – showed four small dishes made of walnut, maple, and ash.
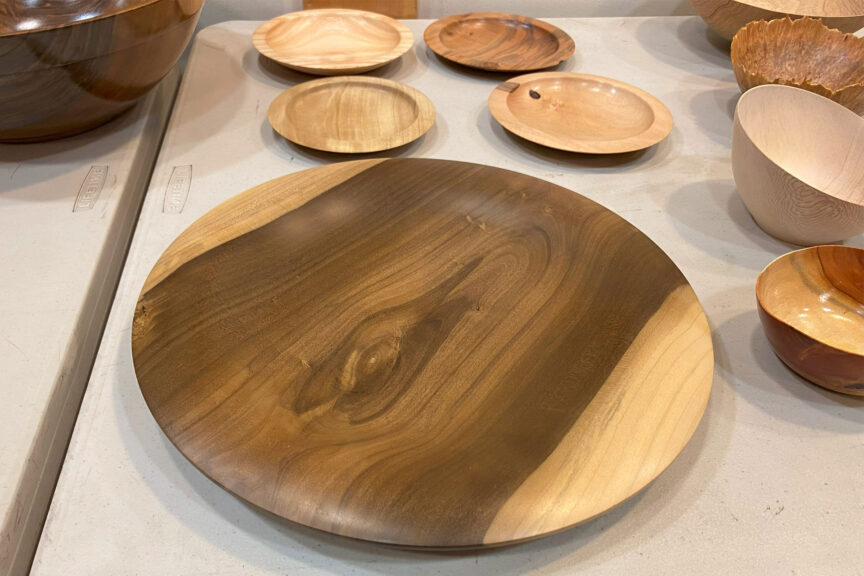
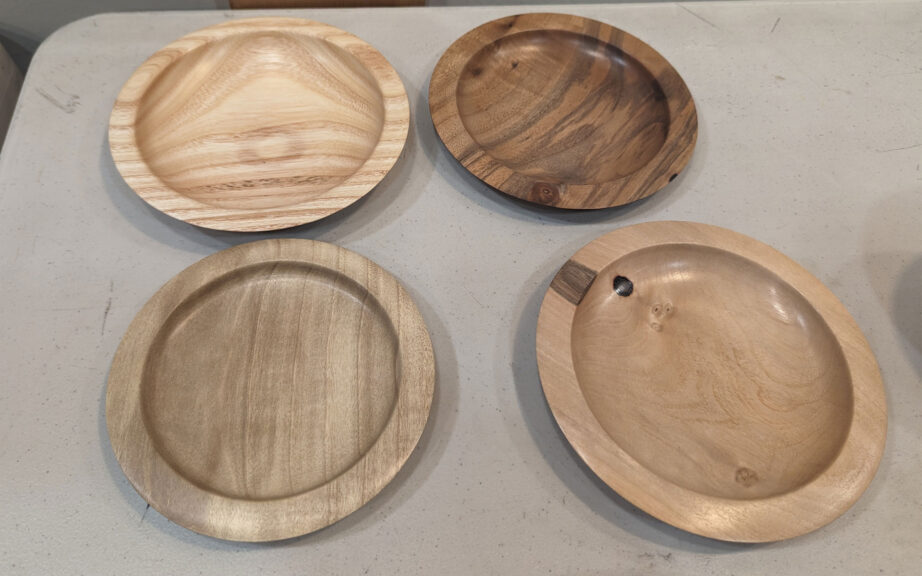
Steve Dahout – brought a tool handle made of Katalox (a.k.a. Mexican Royal Ebony) with a finish of Mahoney’s oil.
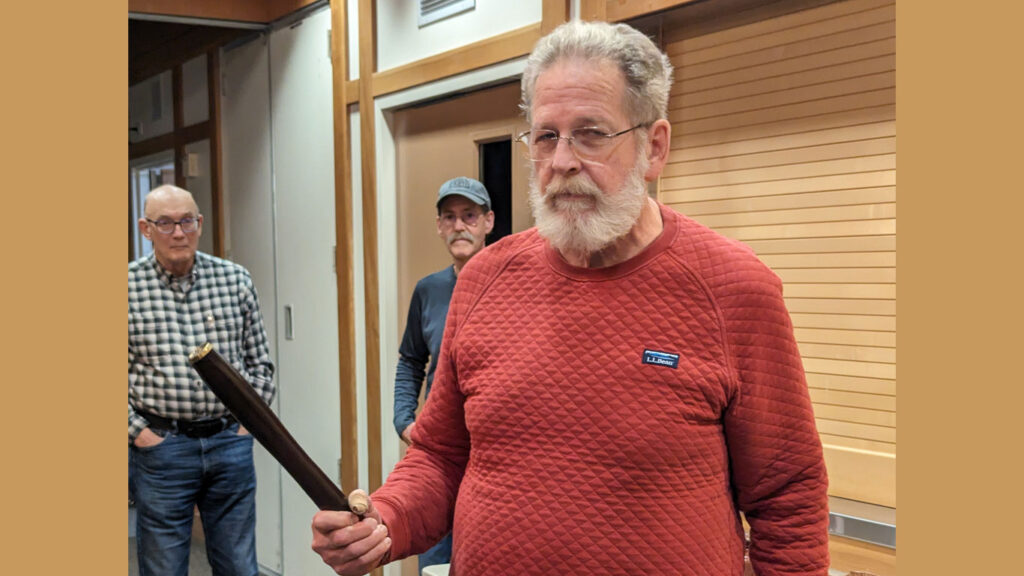
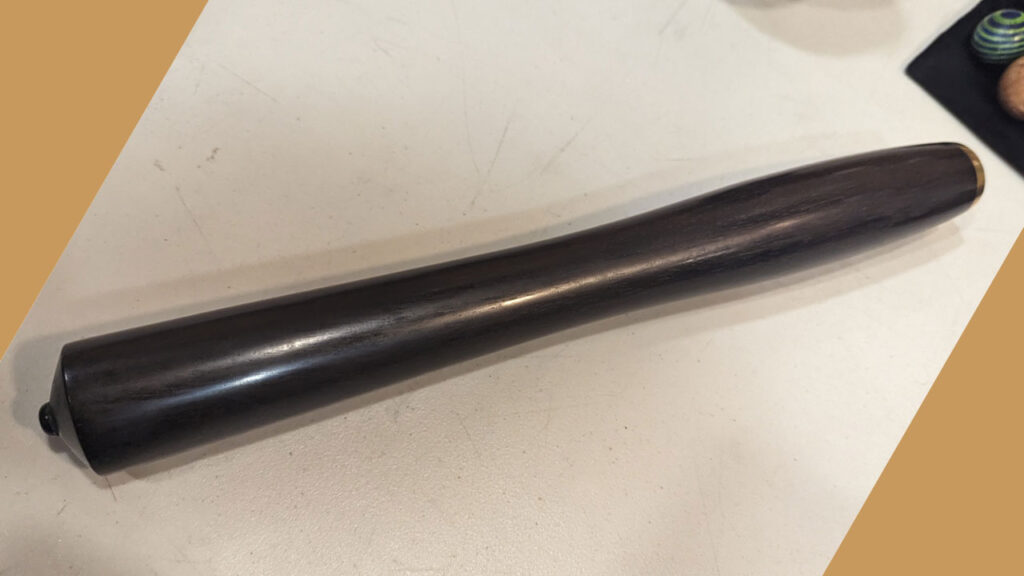
Tom Gaston – showed a redwood burl box, a redwood burl flower pot holder, and a flower vase with a epoxy-plugged brass tube originally part of a brass bed he found on the side of the road.
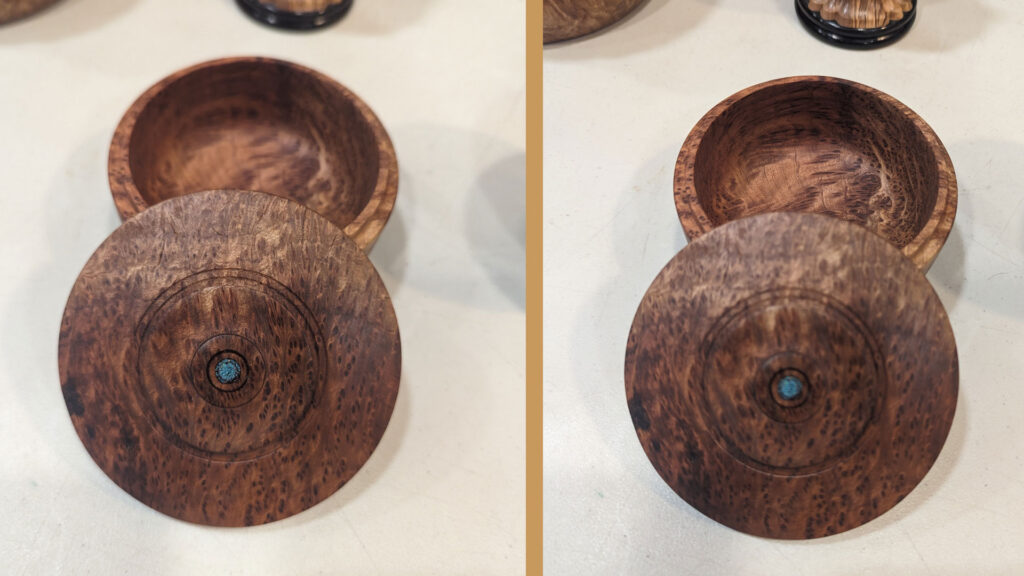
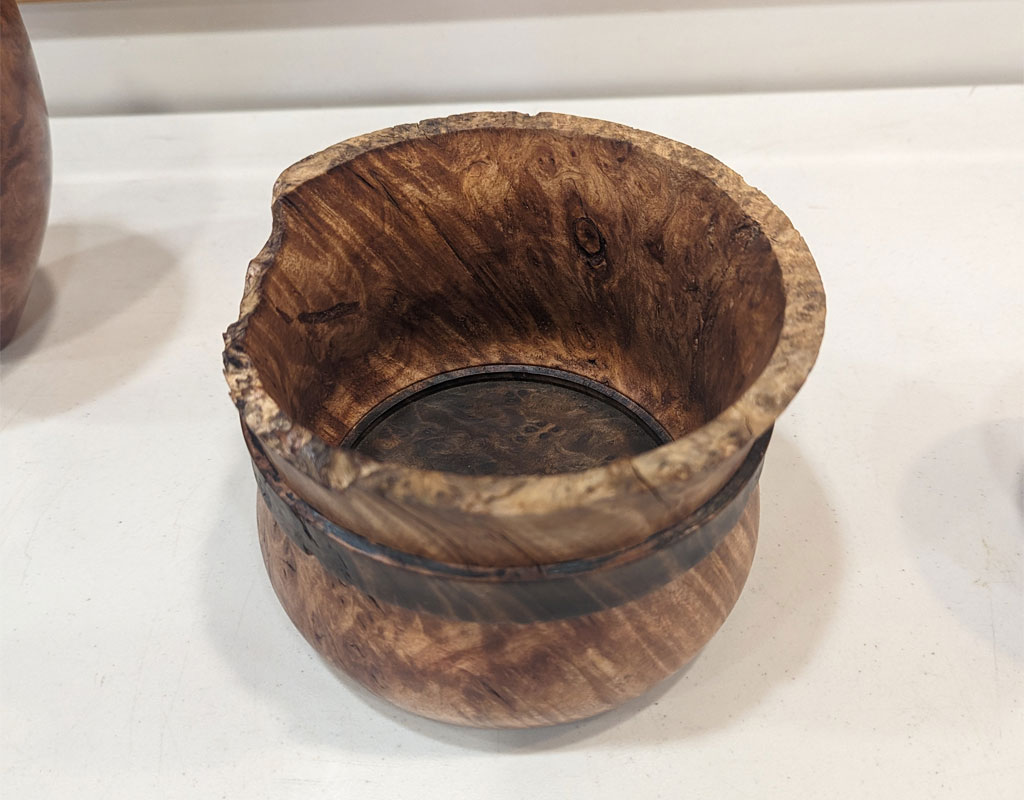
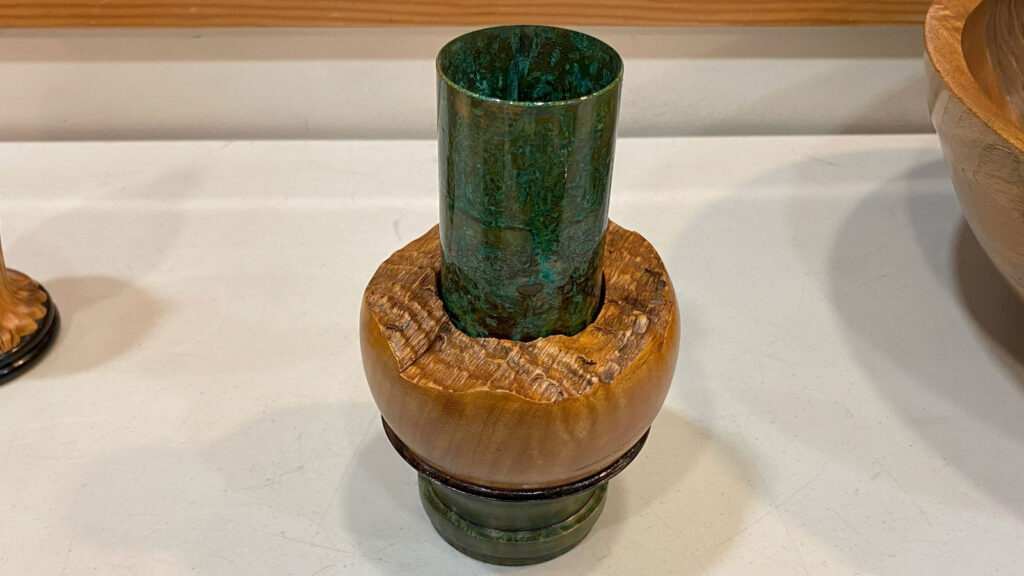
Kelly Smith – showed a box made of Narra which he obtained some time ago at an estate sale. He finished it with Mahoney’s oil and wax. He also brought a walnut dish with nesting spice bowls, a cherry bowl, a tulip poplar bowl, a blue oak natural edge bowl, a madrone bowl, and a mushroom made of almond wood.
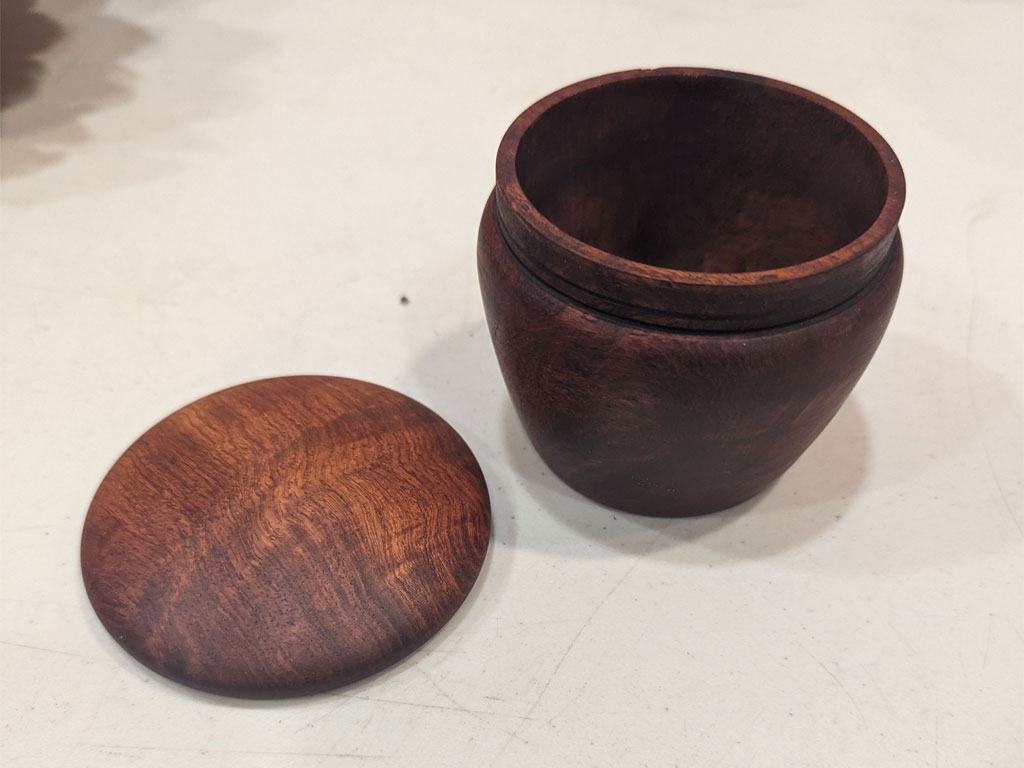
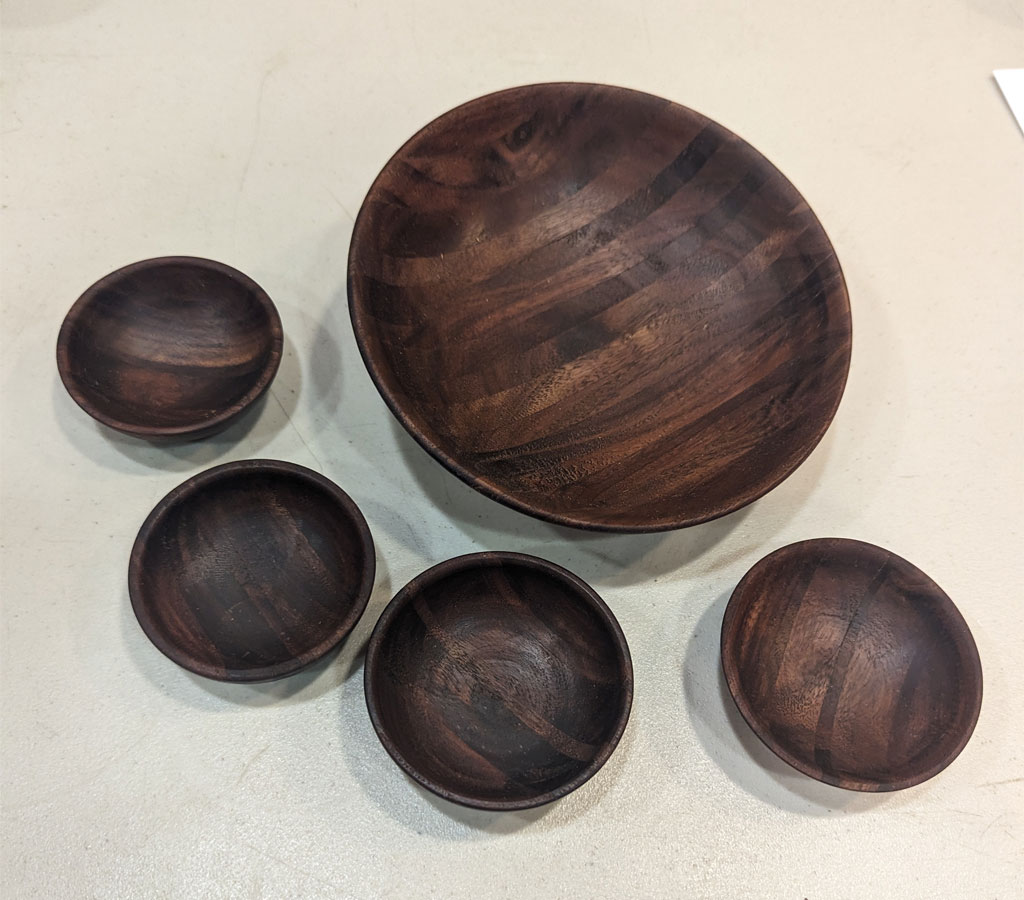
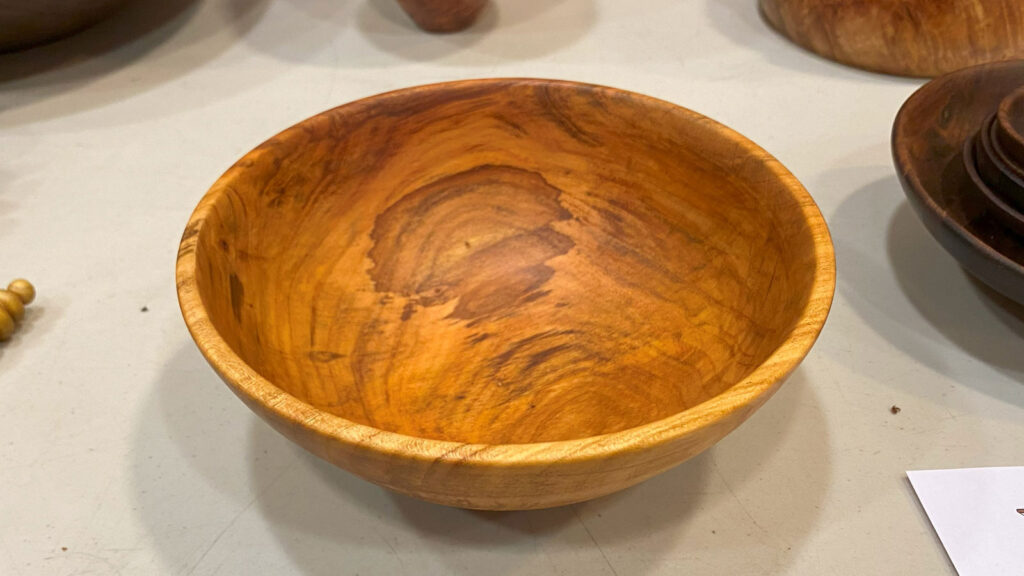
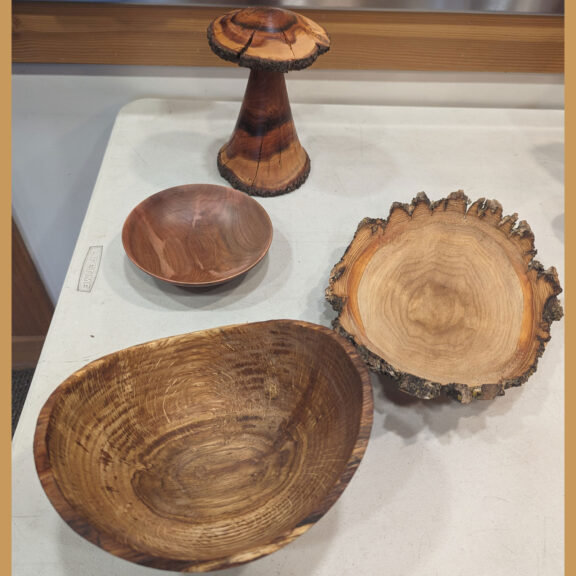
Dale Bassmann – showed an intricate box which consisted of seven piece of several different woods, including: pink ivory, African Blackwood, and betel nut. It was finished with lacquer and buffed. Dale used both his regular lathe and his ornamental lathe to create this box.
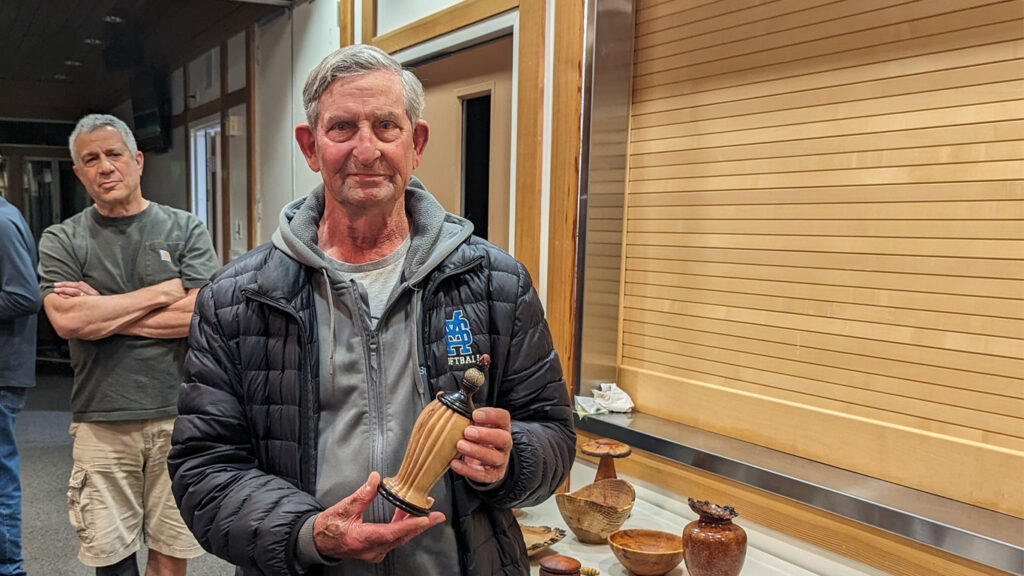
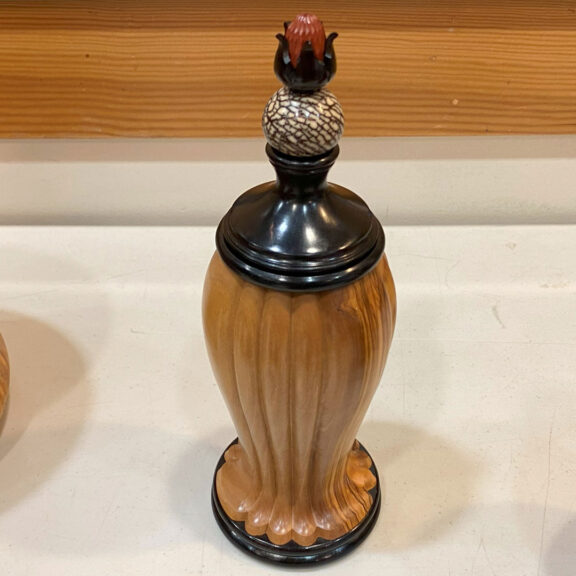
Dan Boehmke – left the meeting before he had a chance to show two walnut bowls and a “mystery wood” bowl.
Who did turn these two items below? Looking for the author names.
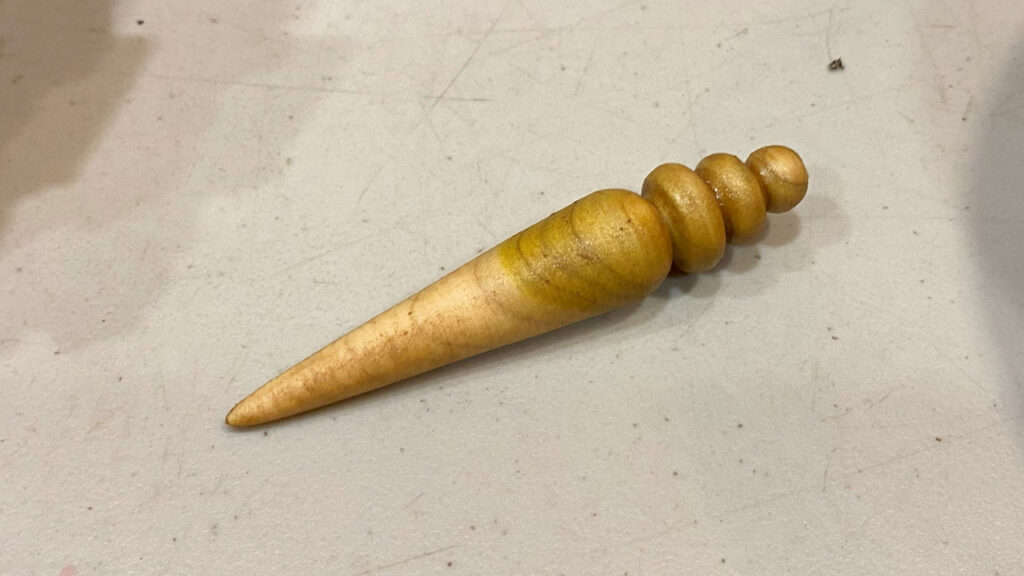
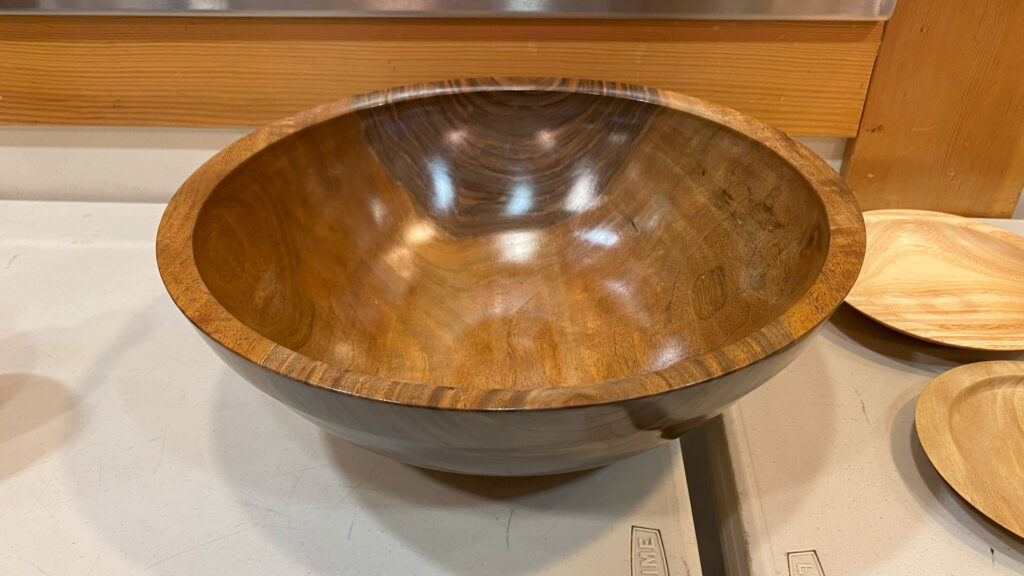
Mike Mahoney Demo Recap – March 10, 2024
By Laura Rhodes
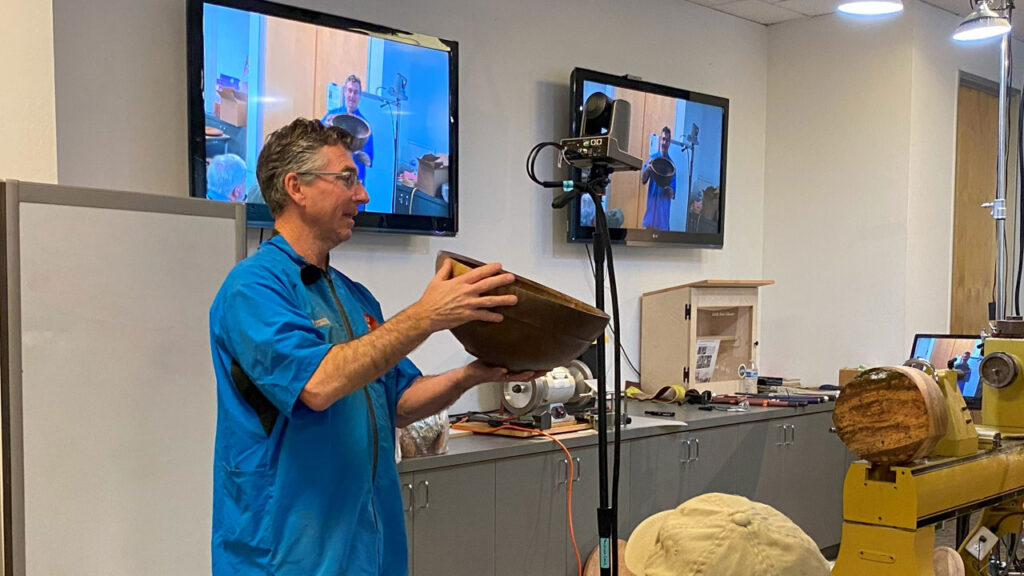
Mike’s demo was held at Maker Nexus in Sunnyvale. Mike first told us about his background and about his business (Mike Mahoney – Bowl Maker). His first woodturning symposium was in 1988. His wholesale business focused on salad bowls. He considers his work his children. He said that when making turned items for the home, one must choose the right wood, at the right scale, and that he really wants his pieces to be used.
He also spoke a bit about finishes, dividing them into two families: first,film finishes, including wax, polyurethane, acrylics, shellac, and paint; then,oil finishes, including: Boiled Linseed Oil, Tung Oil, Nut oil, vegetable oils, mineral oil and Danish Oil. Factors to consider when determining which finish to use include, toxicity, repairability, marketability, skill to apply, and color. He gave his recipe for a varnish finish, 1/3 gloss oil based poly (Varethane), 1/3 Boiled Linseed Oil, and 1/3 Mineral spirits which he uses on items that are meant for display. For items that are used for holding food, his #1 favorite finish is NO finish. His #2 finish is walnut oil because it is cheap, easy to apply and repairable.
Mike first made a platter of valley oak. He then took a large piece of valley oak and cored out two small bowl blanks from the center using the McNaughton coring system. The large outside piece, he turned into a calabash bowl. He turned a hollow form from a piece of red oak burl. He used a Kelton McNaughton tool to hollow out the form. He demonstrated hand chasing threads. Mike then finished by making a thin-walled bowl out of one of the blanks previously cored out. All the pieces he turned that day were raffled off.
Laura Rhodes
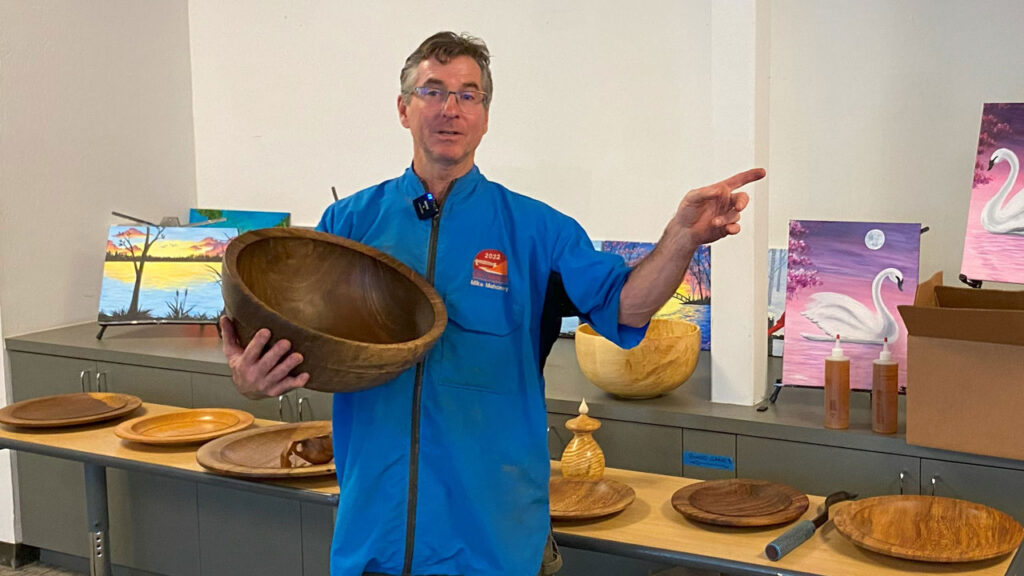
Read an article written by Roman Chernikov — a detailed and engaging overview of Mike Mahoney’s woodturning demonstration, highlighting key techniques and projects. It effectively encourages readers to explore further opportunities to learn from Mike and participate in future woodturning events.
President’s Message
Nothing pleases me more than to see the level of participation at the last two meetings and with the newsletter! A lot of people contribute, YOU are the ones making our club interesting and successful. Keep it up please, anything you do adds up to a whole that is bigger than its parts! I’ve had to miss the last two meets, but can’t wait to get back and see you all again soon.
Claude Godcharles
“As the Wood Turns” by Dave Vannier
I’ve had a few discussions about boiling wood this past month. I was first introduced to the process by Dale Larson in one of his all day demo’s. You can find an article by him in a past AAW magazine. He showed us a few different things, including is eccentric chuck. Pretty expensive, but made turning oval bowls, not just letting them warp, pretty cool. Not sure if would ever do enough of them to justify the price. In addition, Dale stopped and picked up a madrone burl. He demonstrated cutting it up to maximize the figure. Then taking the blank to the lathe and rough turning a piece. Next, he discussed the boiling process. Hard boil for 1 hr for each inch of thickness. Simple to remember.
Since then, I’ve experimented some with it. I’ve got a turkey roaster, and 3 different pots. The smallest works great for a bowl. Next, i can boil a couple of core sets. Finally, I’ve got a 55 gallon drum for big loads. I’ve not used it in quite a while. Haven’t purchased a 1000lbs of madrone burl for a while, and may never do it again. But, i do like to keep the blanks in water before they are boiled. My experiments have been with different woods. Madrone and madrone burl always get boiled. I’ve tried maple, bay, carob, and most recently olive. Maple and bay did dry faster, but I can’t say I really noticed any other differences. Carob, eh same tendency to crack. Olive was interesting. I saw someone talking about how it stopped the cracks. Well, my attempted did get it to dry, but stopping cracks? No such luck.
Note, it does cause a color change, but just on the surface. After returning, I can’t tell the difference. Fighting mold is an issue. You will have better luck if you remove the pieces from the hot water as soon as possible, letting them steam off. Then keep them in a cool low air movement environment for a few weeks. After that just let them dry. One warning! Put the bowls in open side up. Trapped hot air that can be dangerous.
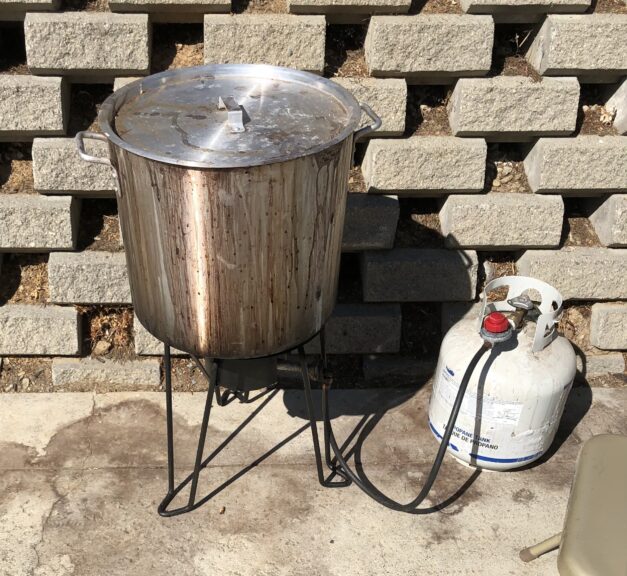
Medium pot ready to boil.
WBW board members and committee chairs
President: Claude Godcharles
Vice President: Tom Gaston
Treasurer: Jon Bishop
Secretary: Laura Rhodes
Member at Large: Fred Colman
Meeting Program Coordinator: Vacant (Claude G acting)
Visiting artist Coordinator: Vacant (Dean Caudle acting)
Anchor seal: Dennis Lillis
Craft Supply: Tina
Librarian: Kelly Smith
Audio Visual: Curtis Vose
Website: Roman Chernikov
Newsletter: Angela, Claude, David, Laura, and Roman.

Leave a Reply