On October 6, 2024 Eric Lofstrom gave an all-day live demonstration to the combined West Bay Woodturners and Silicon Valley Woodturners clubs. The demonstration was held at Maker Nexus in Sunnyvale.
Eric Lofstrom focused on the following topics for the demo:
- 6 basic cuts with the skew chisel
- End grain bowls
- Square Rim bowls
Eric began by telling us a bit about his background. He is in his 27th year as a Physical Education teacher, 23 years at the elementary school level, 4 years at the middle school level. He began his woodworking career as a three-year-old and has been woodturning for 24 years. He initially thought he would become an orthopedic medical doctor but realized that what he really liked was working directly with patients and athletes. He has a degree in sports medicine. This background helps explain Eric’s focus on body mechanics while turning.

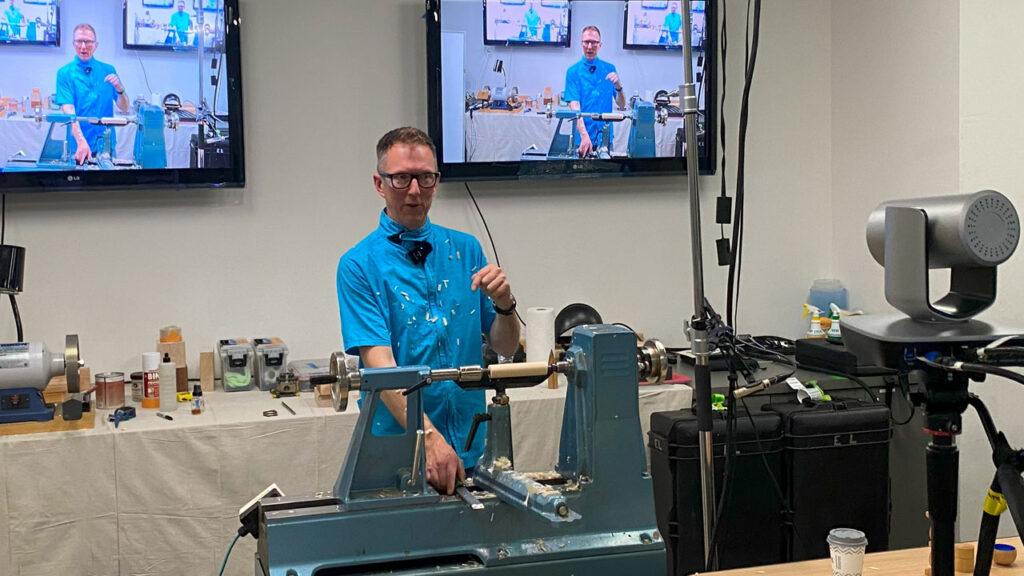
He warmed up and calibrated himself to the lathe by speed rounding out a square blank of radiata pine. He did successive steps of peeling cuts with the skew chisel, then smoothed out the cut and made it cylindrical by gliding right to left and left to right, producing one long thin shaving. He held the skew choking up on the handle with his right hand and keeping the end of the handle against his hip. Later in the demo, he would go over in detail each of the body motions needed to create these cuts.
Eric spoke about his woodturning artwork forms, including: his multi-axis raindrops; end grain namaste bowls, breathing boxes; and spinning tops. Examples of these forms can be found on his website, www.ericlofstrom.com. Some of his pieces, such as the miniature (sub-sub-dime-sized) spinning tops, require fine body (not arm) control. Eric often turns either barefoot or with super flexible “barefoot” shoes with insoles to achieve this.
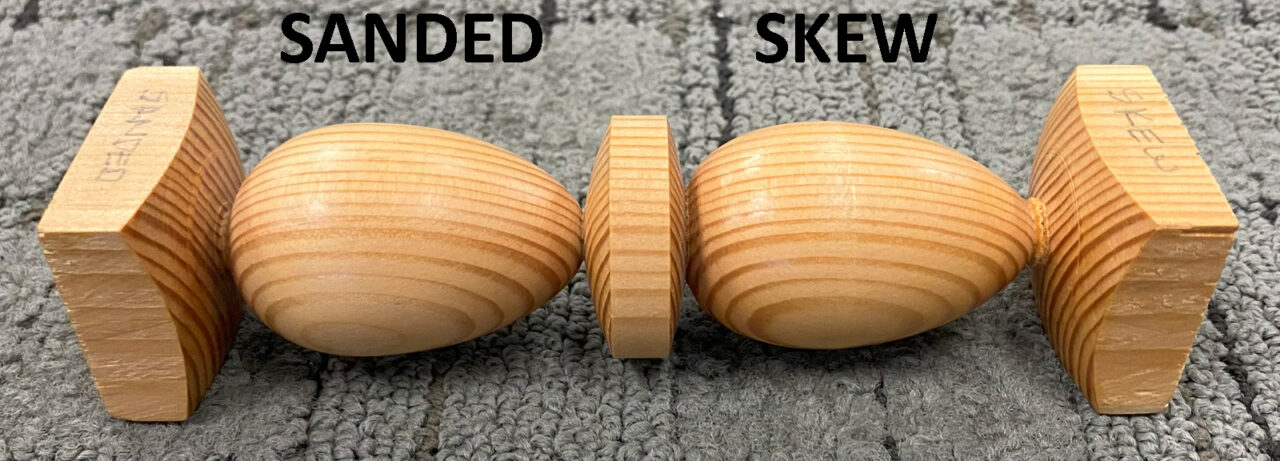
Eric is a master with the skew chisel and has his own signature skew that he manufactures in collaboration with D-Way tools. He discussed and demonstrated each of the following skew chisel cuts:
- Peeling Cut (peel and skim)
- Planing Cut
- Paring Cut (across the end of the fibers)
- V-cut
- Beading cut (rolling cut)
- Scooping cut (coving cut)
Eric’s skew has a radius edge – almost horizontal at the toe, about 45 degrees at the heel. He has his tool rest set about ¼” below center when using it. He extends the AAW “ABC” mnemonic with additional steps:
- A – anchor
- B – bevel
- C – cut
- D – directed
- E – evaluate
- S – shavings (tell us a lot about the quality of the cut)
For the peeling cut, he had us stand in place and mimic his body motions to dip, straighten then bob for peeling, then glide left and right by shift the body weight from left foot to right foot (and vice-versa) to skim the surface while maintaining a fixed distance from tool rest to the workpiece, making a cylinder.
For the planning cut, the skew is held at a slight angle. Using a slow feed rate, this should produce light, corkscrew shavings, with feathered edges on both sides. One should be mindful to glide (not rub) the bevel. Be careful to only contact the wood in the lower 1/3 of the edge to prevent a catch.
Eric uses a paring cut to clean up the end grain on a spindle turning. He slices the wood with the long point down with the edge vertical to the surface.
A V-cut scores the fibers. He starts the cut in an arc, rotates and swings and end the cut vertical and perpendicular to the wood.
Eric demonstrated the rolling cut by making an egg. He uses the short point of the skew. The skew can also be used to make shallow coves using the scooping cut.
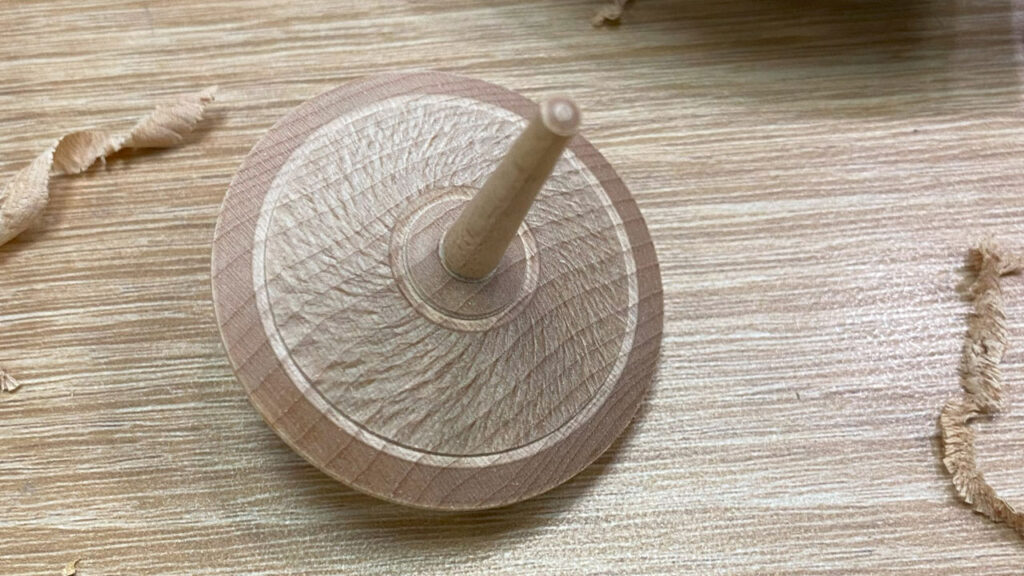
Eric put all the skew cuts together in a demonstration of turning a spinning top. Unlike many turners, Eric turns the handle of the top nearest the tailstock. This is so he can add embellishments to the visible side of the top (such as with the demonstrated chatter tool).
Eric spoke about sharpening the skew. He has a YouTube video on sharpening his signature skew. The basic guideline is the bevel length of the skew should be about 1.5 times the thickness of the shank. After sharpening on the grinder, he hones the skew on a DMT Dia Sharp Xfine 9micron 1200 mesh diamond card and then strops it using emery compound.
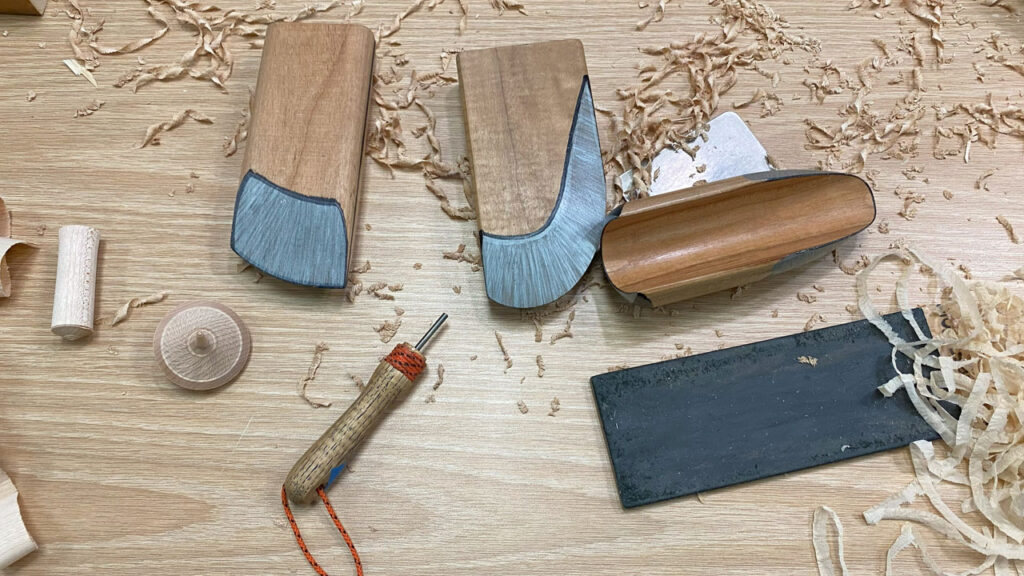
To achieve a long-lasting cutting burr on his scrapers, he uses a diamond card to take off the burr from the grinder and then uses a burnisher to create a better-quality burr on the tool. The burnisher is made from a solid carbide 1/8” shank tile cutting router bit. Only the shank of the bit is used, the “business end” is buried in the burnisher’s handle.
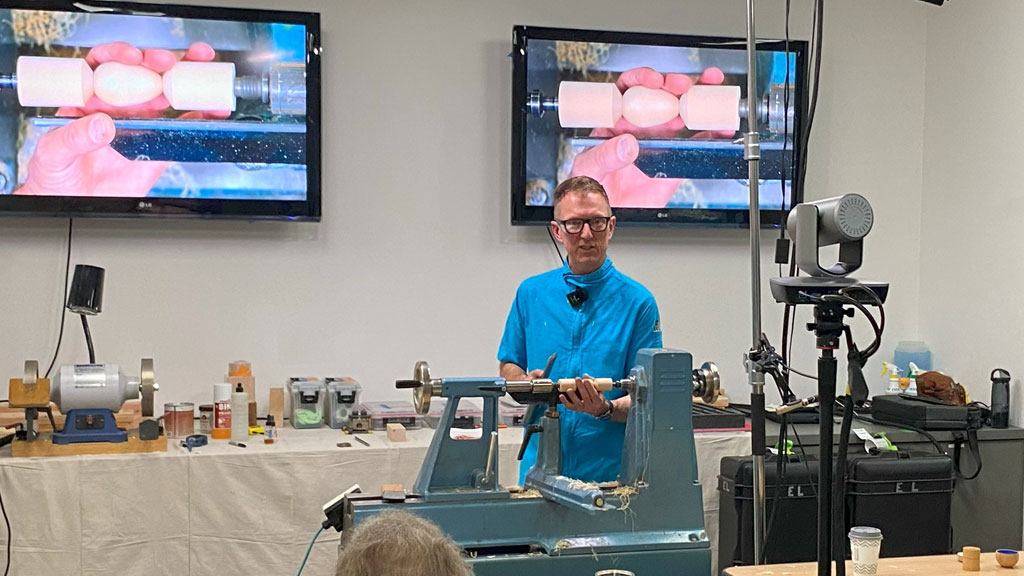
Eric spoke about the inspirations for his artwork, at times becoming very emotional. He demonstrated making one of his Namaste end-grain bowls. The Indian greeting, “namaste”, can be translated as “the inner light in me honors the inner light in you”. He strives to make the interior shape of these bowls reflect light from its surroundings (as if they were lit up from the inside) with a slightly turned in top lip. He prepares the interior for paint with a layer of dewaxed shellac and a shellac-based primer.
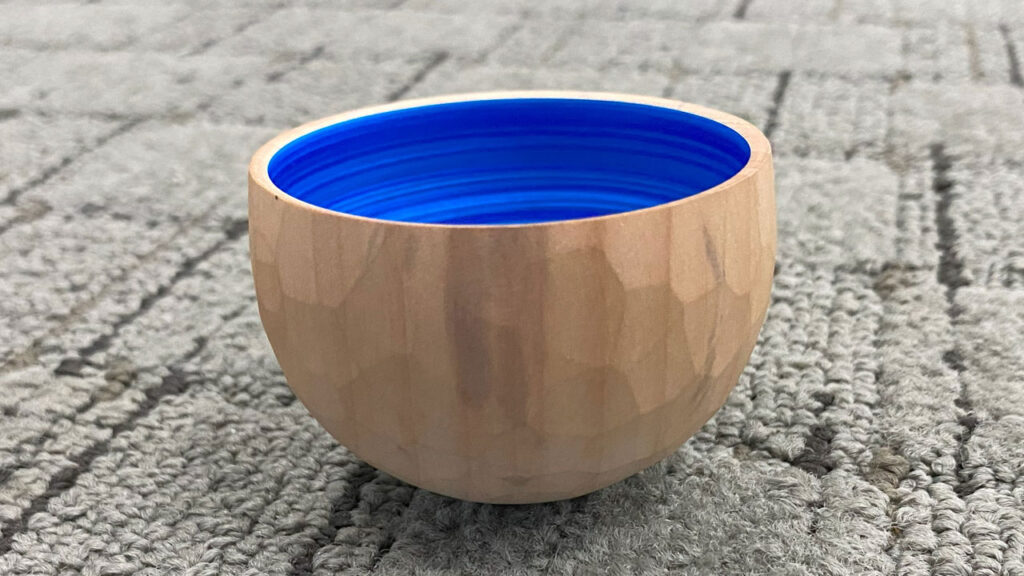
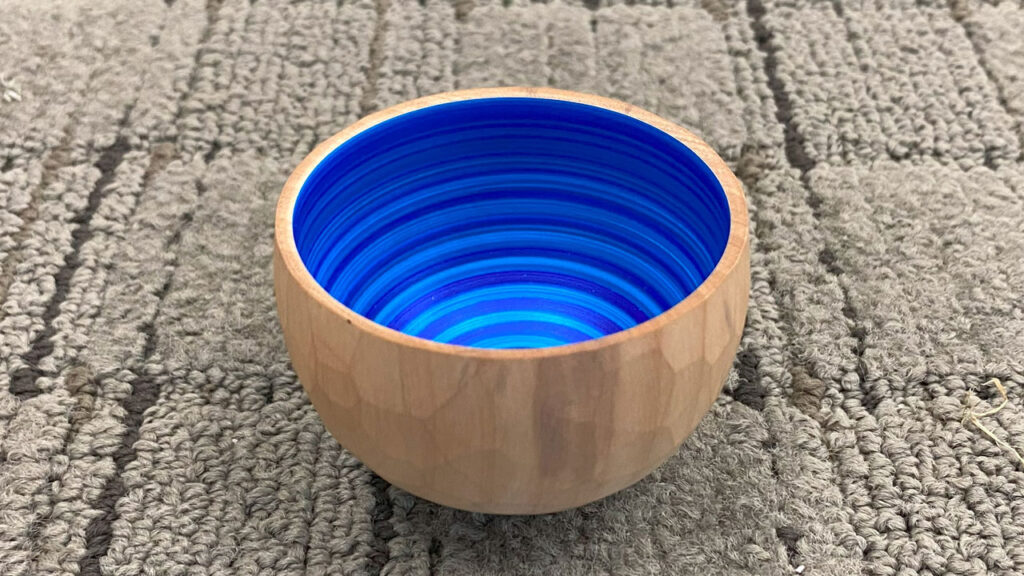
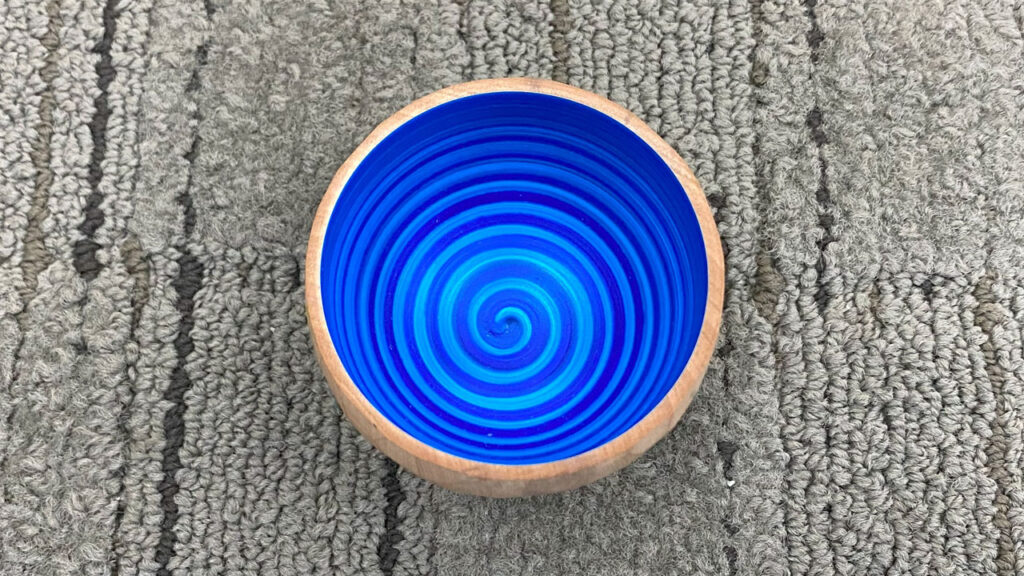
Eric Lofstrom builds visual depth in the interior of the bowl with successive layers of acrylic paint spiraling from the top down to the center of the bottom. He uses acrylic paint from Golden. He uses a good quality paint brush from Filbert. He often finishes the outside of the Namaste bowls by either wire brushing using a Forney medium or fine stainless steel wire brush or by faceting the exterior using a disc sander.
He finished up the demonstration making a square rim bowl, that featured “ripples” radiating out from the center small bowl, like a pebble creates when tossed into still water.
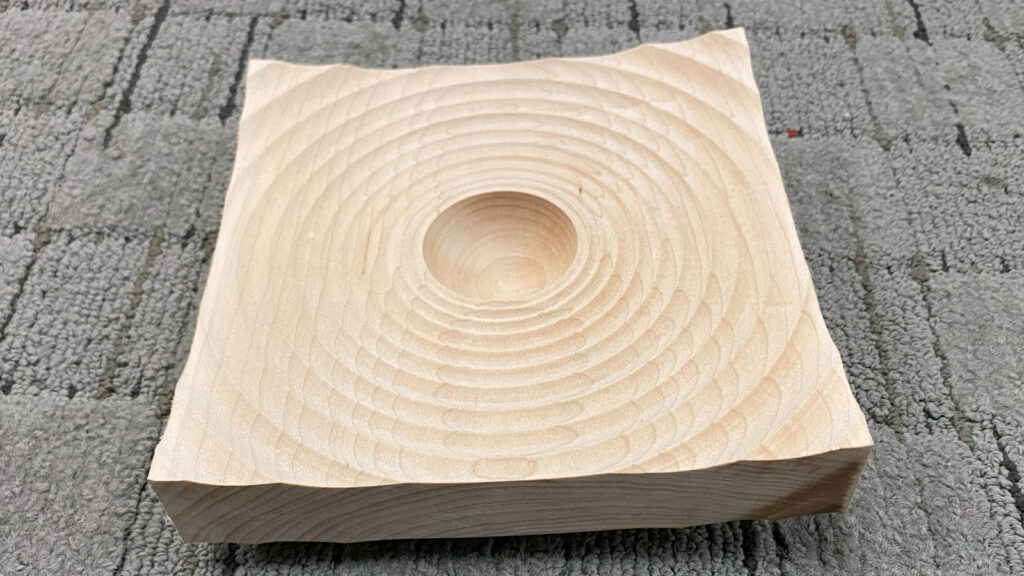
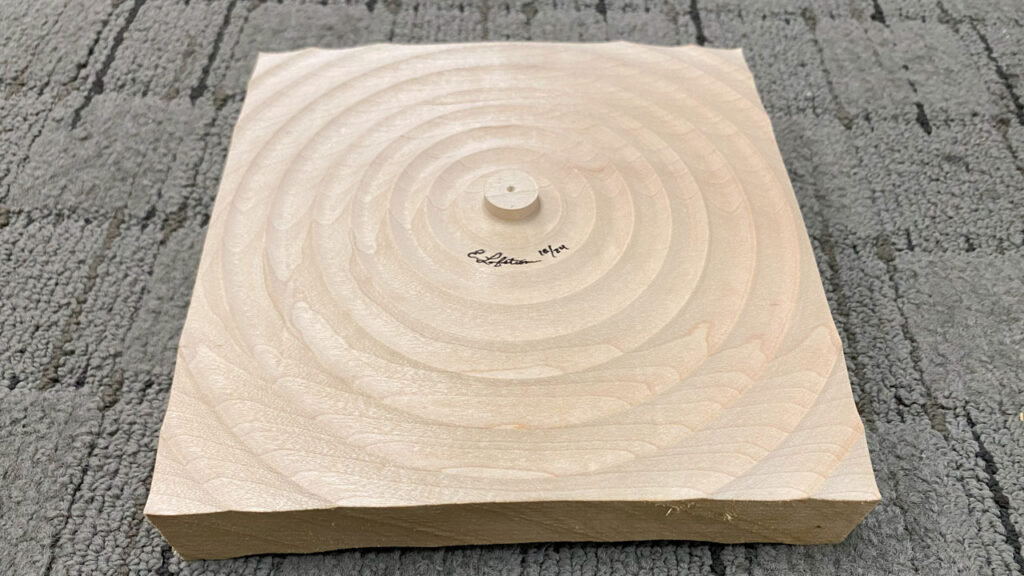
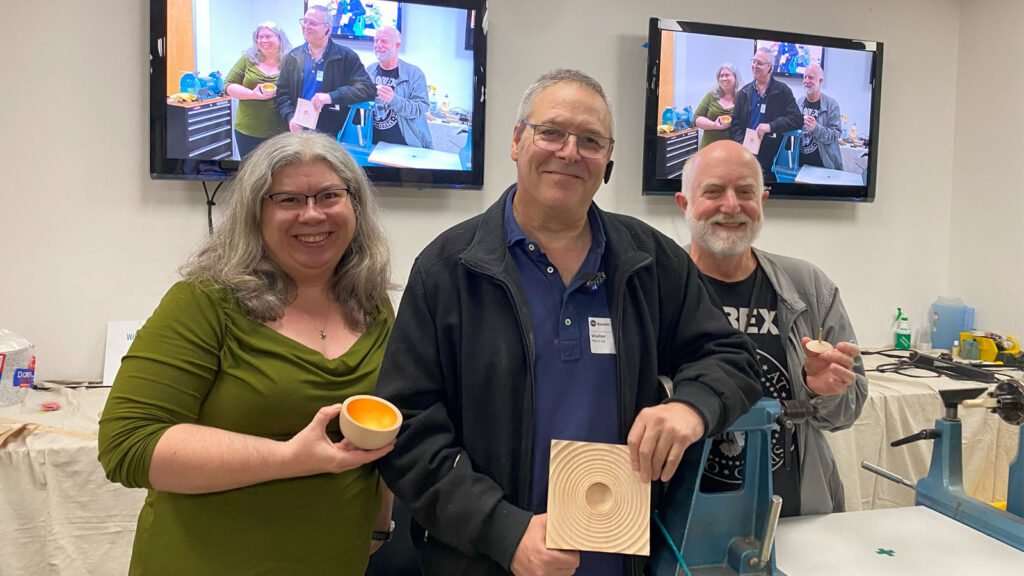
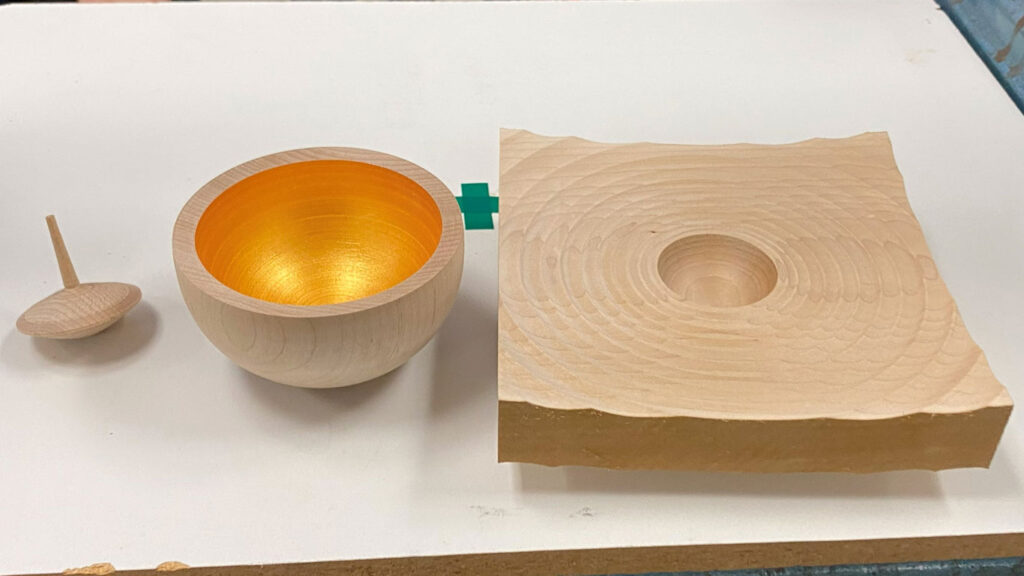
The Ripple bowl still has a tenon that needs to be removed by a raffle winner. Lucky winners: Angela Gunn, Kevin Lee, Vic Mitnick.
Leave a Reply