West Bay Woodturners Newsletter is a monthly update on the club activities. This free resource is available to beginner and professional woodturners.
Next Meeting
Wednesday November 20,
7 pm at Bridges Church,
625 Magdalena Ave,
Los Altos 94024

Program
November: So you wanted a handle on that bowl? Demo by Tom Gaston.
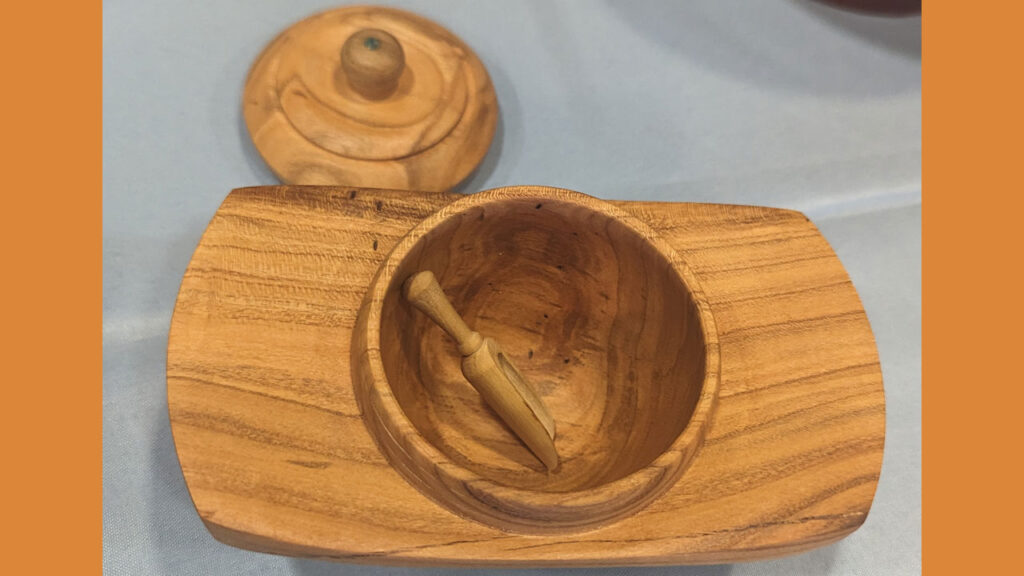
President’s challenge:
November: Egg shape, any tool!
Inspired by Eric Lofstrom‘s October demonstration where he showed turning eggs by practicing the skew-chisel skills.
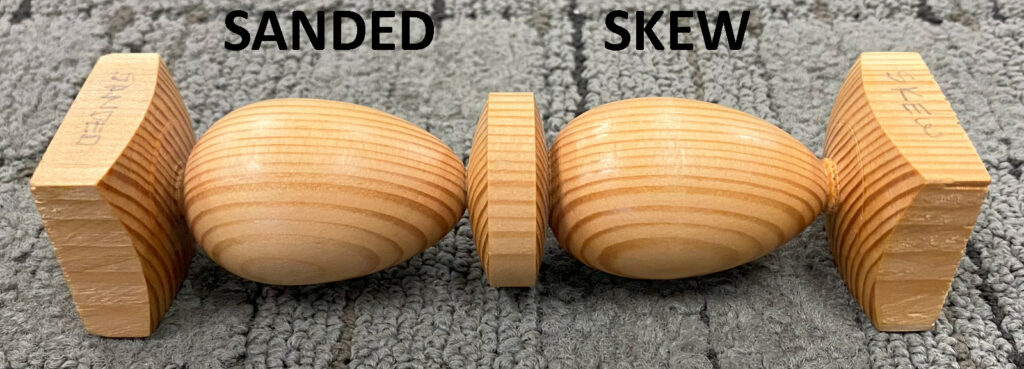
Upcoming Meetings and Demos
- December Holiday Party — details to follow
- January 2025: TBD, but most likely our traditional extended show and tell
President’s Message
It’s great to see all the work and contributions at the last meeting. I was not there, but the newsletter gave me a pretty good idea of the demo, show & tell and other bits. Which prompts me to recognize the amazing work that our newsletter team puts in. That would be Roman, Angela, Laura, David… Please take a second to show them some appreciation when you have a chance! The new format and team work environment is amazing. It would be great to see more written contributions from you. If you have a story, anecdote, adventure from the shop to share, just jot it down and send it to the newsletter team. It doesn’t have to be a novel, and since there is limited time to share details at the meeting, this could add to our community knowledge base. We could also pull some topics from Slack to share with a wider audience… Food for thought!
Claude Godcharles
Last Meeting Review
Wednesday October 16, 2024
Woodturners newsletter notes by Laura Rhodes, pictures by Angela Gunn and Roman Chernikov
Announcements
- The meeting was led by Tom Gaston because Claude was out of town.
- Guests:
- Manisha Jain – took Tina’s Palo Alto Adult School turning classes.
- Nominations are still open for the upcoming WBW board positions. So far we have a single nomination for each of the four elected positions:
- President – Jon Bishop
- Vice President – Tom Gaston
- Treasurer – Jim Koren
- Secretary – Laura Rhodes
- There was a good turnout (28 attendees) for the Eric Lofstrom demo on October 6. The session was recorded and should be available soon for club members.
- Dave Vannier spoke about a class that he took at Trent Bosch’s shop in Fort Collins with Jacques Vesery, one of the world’s best wood artists with respect to embellishments and paint. Day 1 of the class was about form, day 2 about texturing, and day 3, painting. Dave is trying to get Jacques to teach a class to the club, maybe next year.
- Kevin noted that SVW needs a demo for their November meeting.
- Bob Bley has dust collection hoses for sale.
- Jon Bishop, Treasurer, noted that 2025 WBW dues are now being accepted – $35 if you pay before March, $40 after.
- Dean Caudle has 99% isopropyl alcohol available.
October Program: The exciting world of Scrapers by David Vannier
Dave started out by showing his PPE that he uses for turning, including a powered respirator with face shield. He noted that a face shield will NOT stop a 20 pound wood blank coming off the lathe from injuring your face. Always set your lathe speeds appropriately for the sized piece that you are turning. A rule of thumb is Diameter (in inches) X RPM = 6000 – 9000. The respirator he is currently using is the SR 500/570 Air-Purifying Respirator, https://woodturnerswonders.com/products/sr-500-570-air-purifying-respirator. Not cheap, but neither are your lungs or the doctor bills.
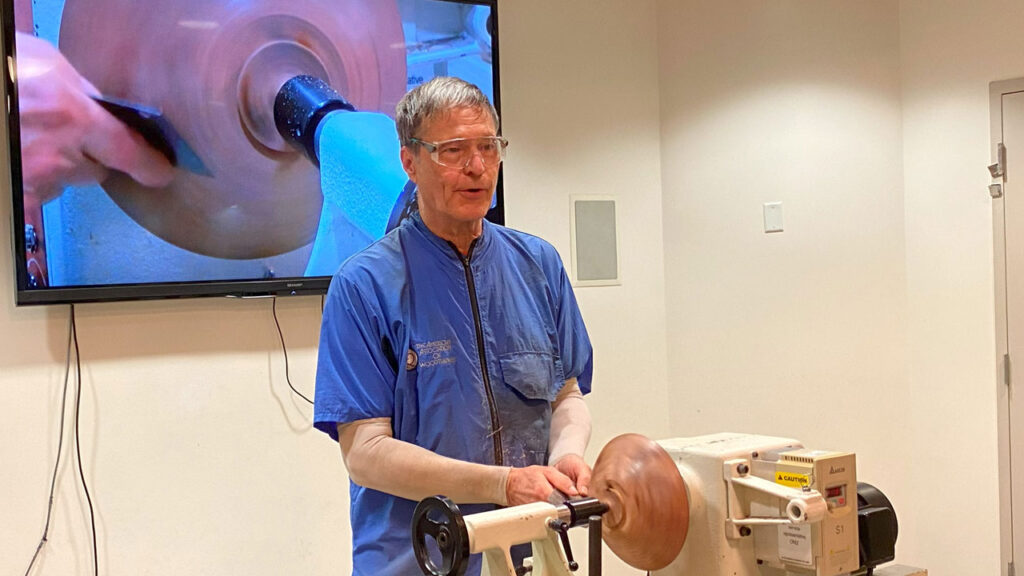
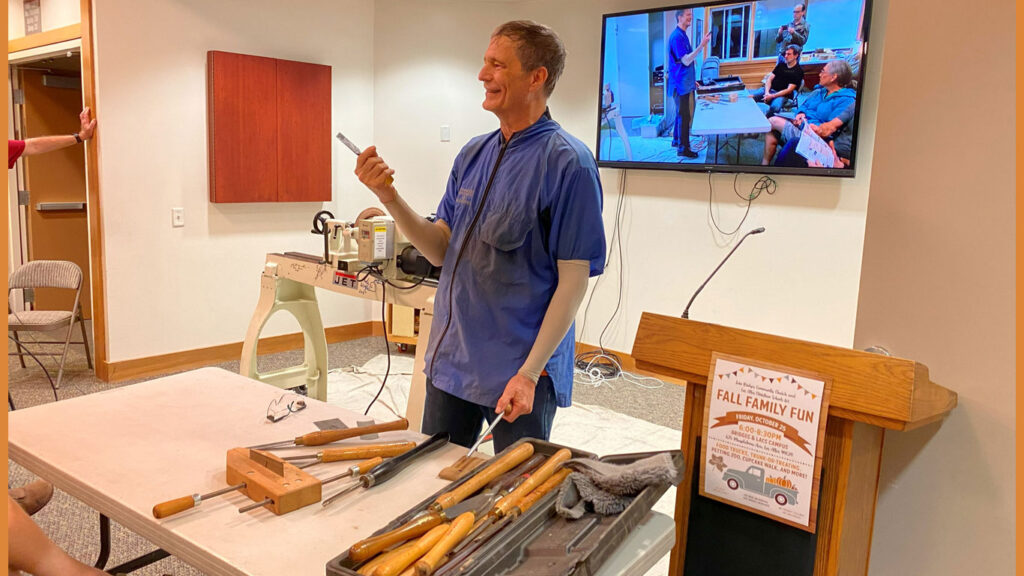
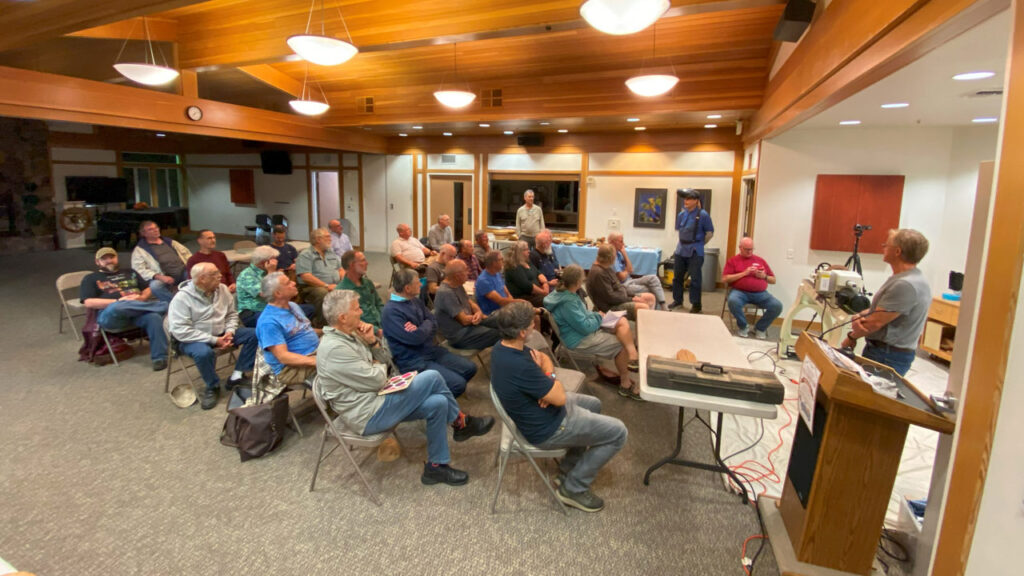
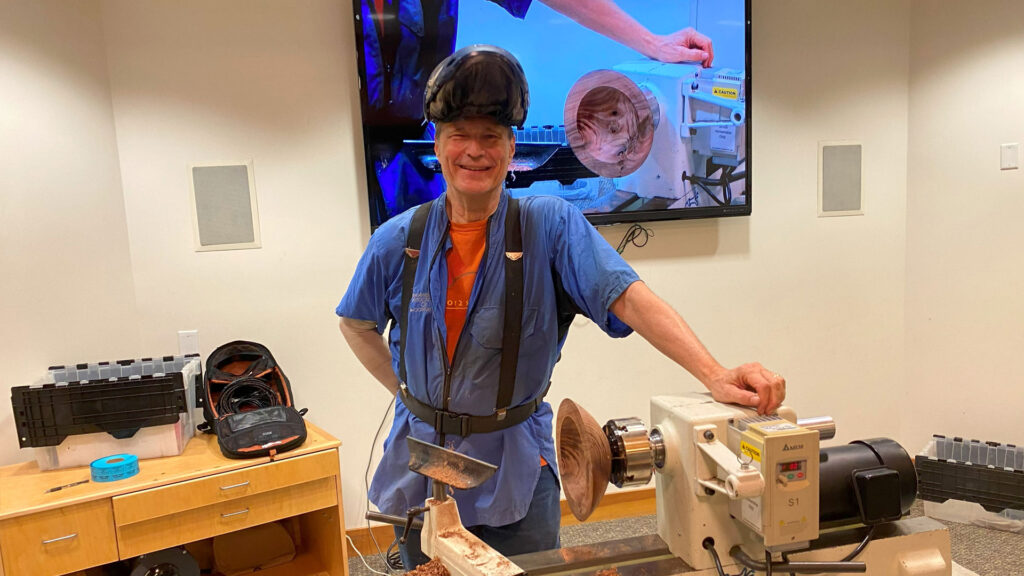
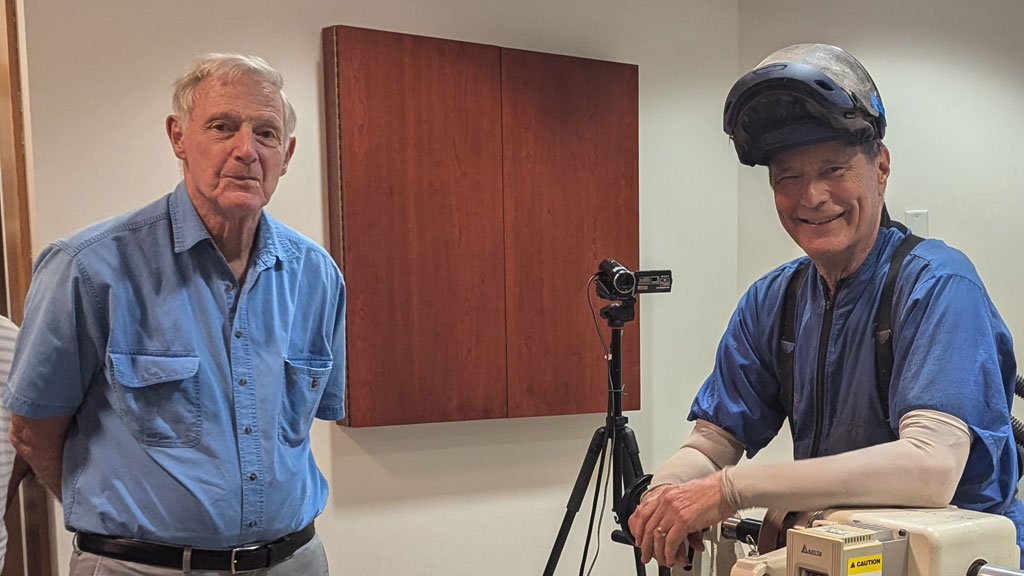
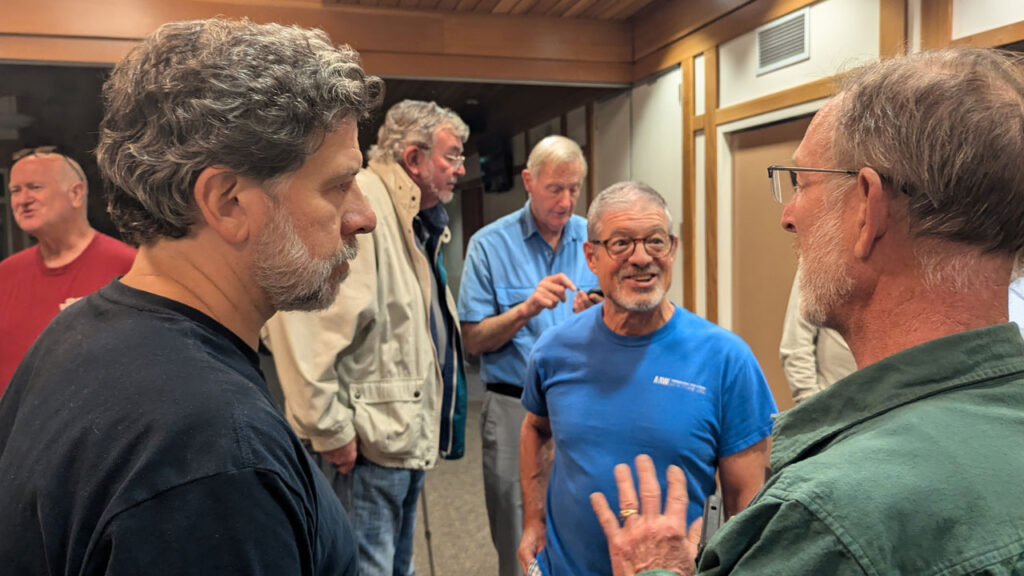
Dave brought a large toolbox filled with his collection of scraping tools. He indicated which ones he likes (and uses) which ones remain mostly unused. He said that a skew can be used as a scraper, but not an oval skew – use a flat skew that will lie flat on the tool rest. Dave uses cabinet card scrapers to scrape the outside of his bowls. His favorite card scraper is a .032” flexible one from Highland Woodworking. Dave sharpens his card scrapers using a chisel rather than a burnishing rod. He showed a box scraper with a profile that makes is good for cutting the parallel walls of end grain boxes. Dave does not like round nose scrapers but rather bowl scrapers with a French curve profile. He also uses a square end scraper. He showed Cindy Drozda’s Vortex tool which is round on the bottom and flat on top. This tool does not cut with the tip, but rather scrapes with the sides. Cindy uses this tool on her finials.
Dave uses Glenn Lucas’s scraper angles as a guide to grinding his scrapers – negative rake 66 degrees, standard 33 degrees.
With some woods, scraping is better than cutting. Some examples are burls and other gnarly woods.
Dave also demonstrated the use of the bottom feeder bowl gouge which has a very step grind with almost no wings. This tool is good for the bottom of bowls and for flat surfaces.
Presidents Challenge: Turn a pen
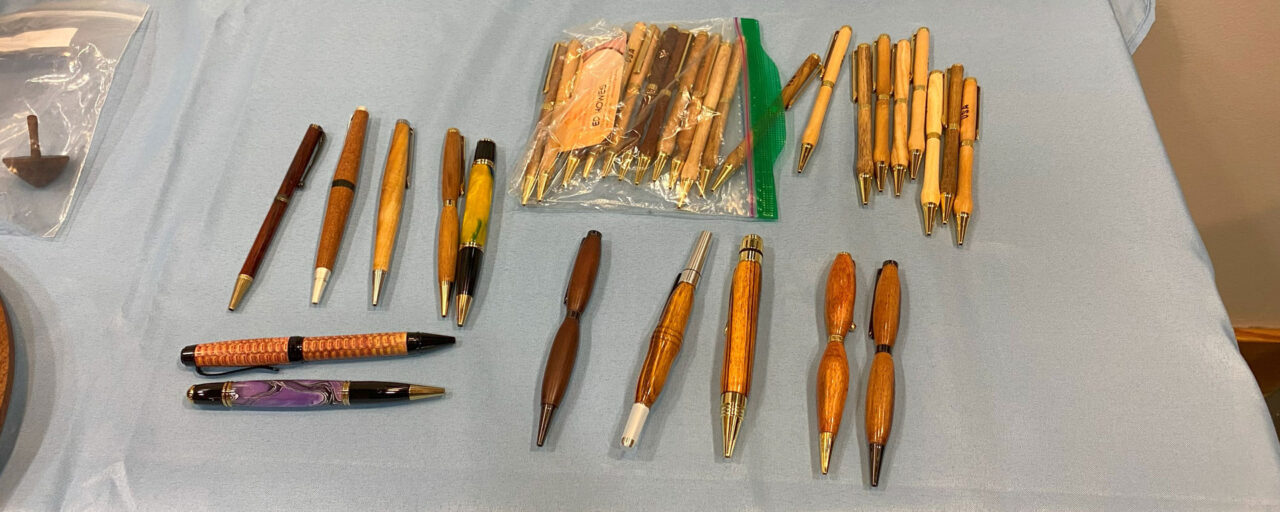
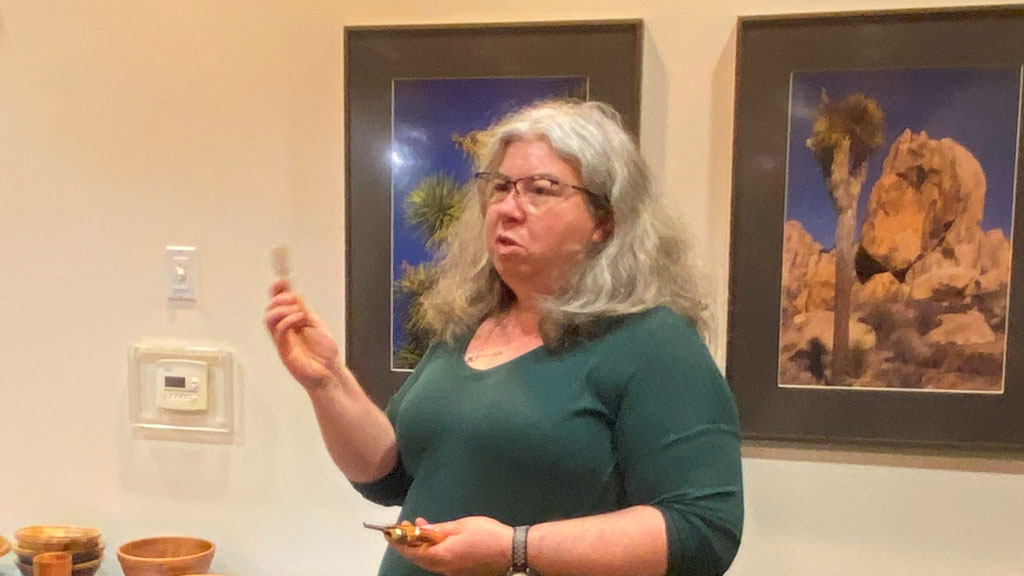
Angela Gunn turns lots of pens. She showed a selection of different pen styles that she turns. She noted that using Doctors Pen Plus results in a finish that feels like wood. Although many pen kits look similar, there is significant variation in quality. She gets most of her pen kits from Penn State.
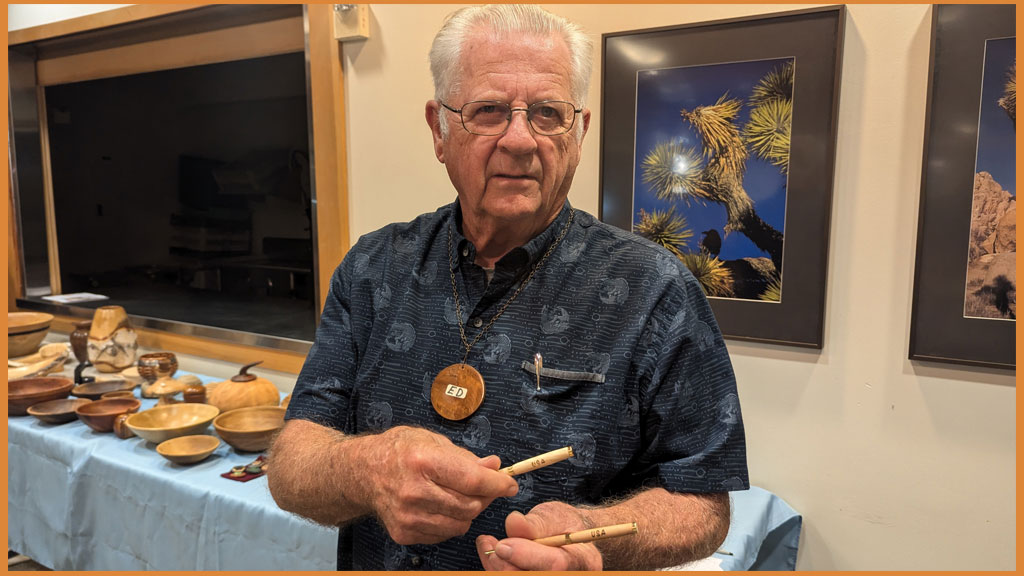
Ed Howes made some contributions to the “Pens for the Troops” program. He noted that 3 generations of his family turn pens. He laser-engraved the pens with “USA”.
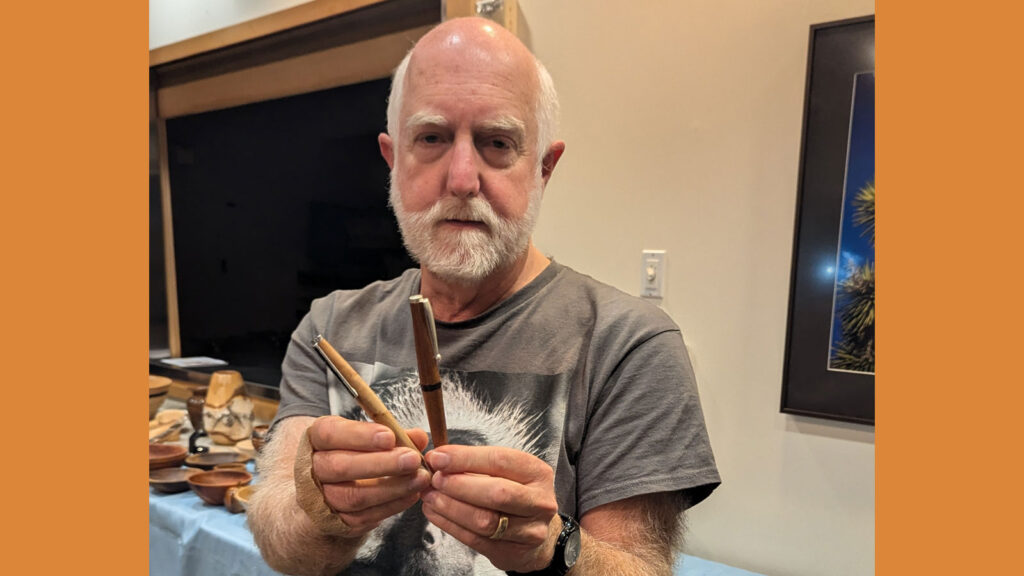
Vic Mitnick made 2 pens. Although he starts out with a slim-line kit, he customizes them with his own band and uses just a single piece of wood.

Jerry Galli showed the slimline pen from his demo last month and an acrylic twist pen with a Parker refill, sanded and polished to 12000 grit with no finish.
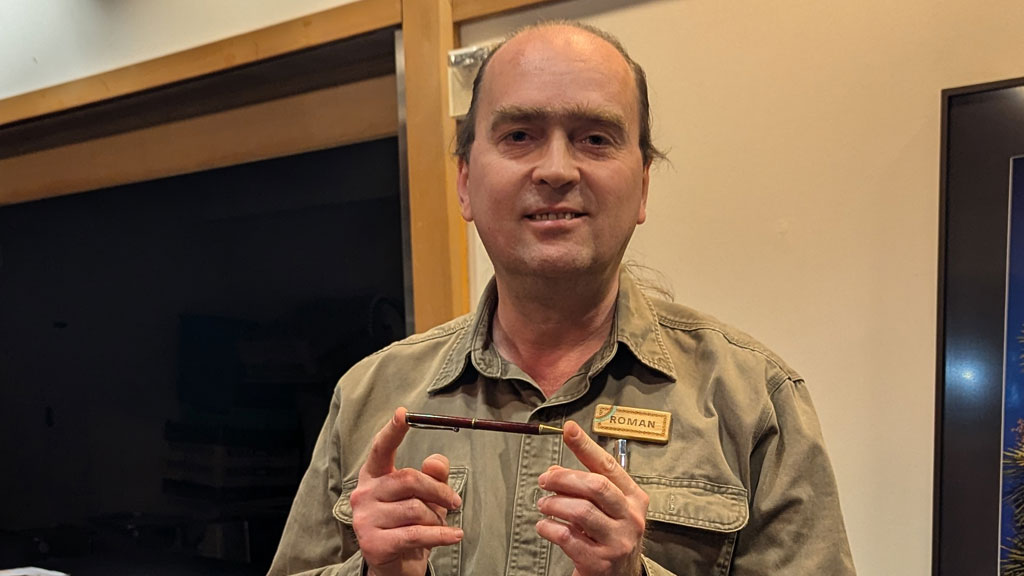
Roman Chernikov made a cocobolo straight line pen. He found the wood grain difficult to finish because of the large pores. He used a CA finish.
Visit READ N TRY – Roman’s website about chip carving, whittling, and woodturning.
Show & Tell:
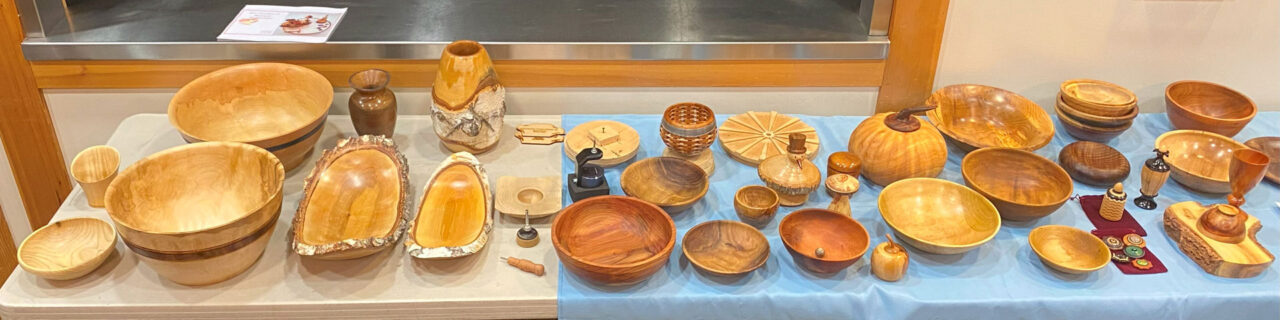
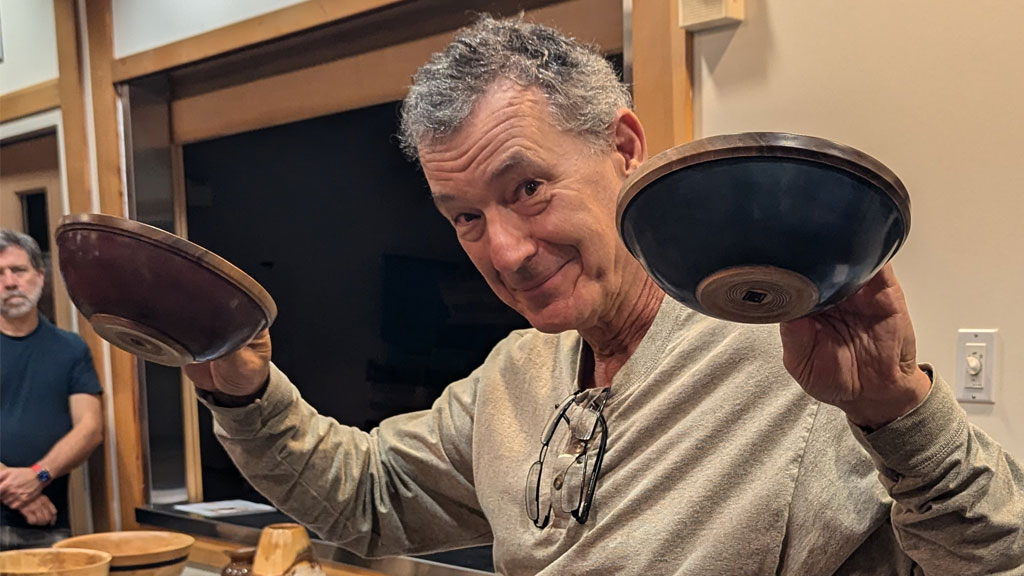
Jon Bishop made several maple bowls and walnut bowls embellished with milk paint. He once-turned a large bowl from green bay laurel and finished it with Tried and True. It has already warped. He took an idea from Richard Raffan and turned a small Bay Laurel bowl with a foot exactly sized for the chuck, so it did not need further turning after the inside of the bowl was hollowed out.
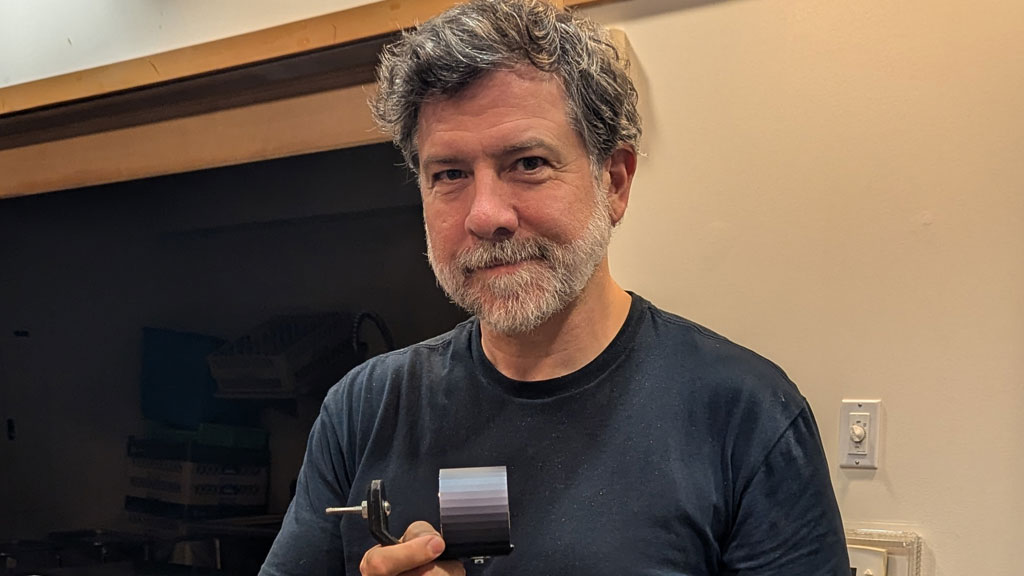
James Craig showed a mount he made for his Laser Pecker engraver. It was 3-D modeled and then 3-D printed. It’s designed to be held in his drill press.
Tom Kenyon is known for his open-segmented turnings. Lately, he has focused more on his metal-working skills in creating kinetic wind sculptures. He has combined these two talents with the creation of open segment wood containers with a decorative metal band and a metal base. Tom has built custom jigs for gluing up his wood segments and custom molds for metal spinning the band and base. He showed a container with 22 gauge aluminum band and base. The metal pieces are attached to the wood using epoxy. He hopes to expand his repertoire to include copper and brass now that he has refined his technique.
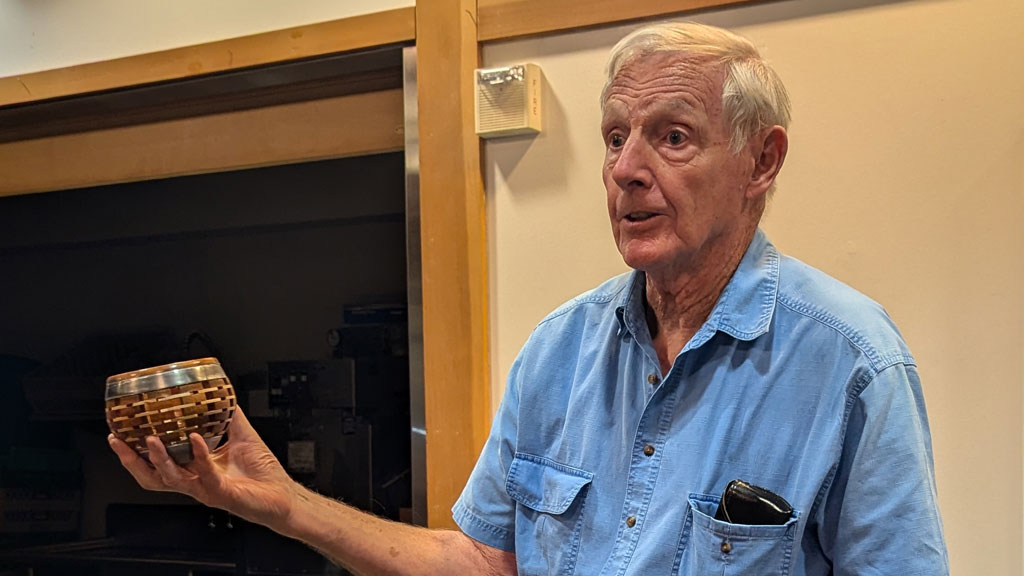
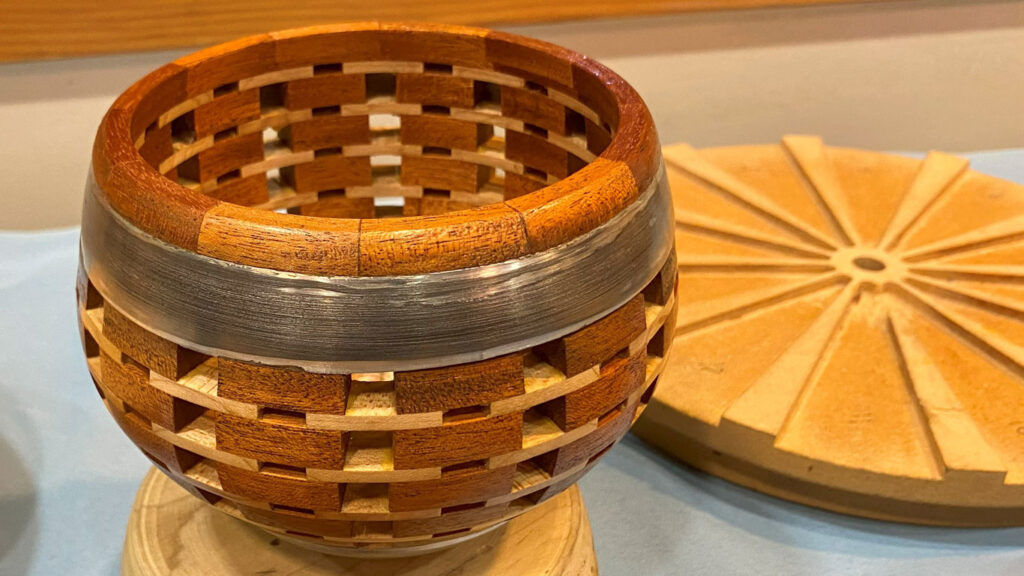
Jon Sauer showed a box made from bamboo and African blackwood, turned on his Rose engine lathe. He made it back in 1995 and sold it and then found it on an auction site two years ago and bought it back. Jon also showed a selection of custom designed buttons that he creates for button collectors. Visit Jon’s website: https://www.jonsauer.com/
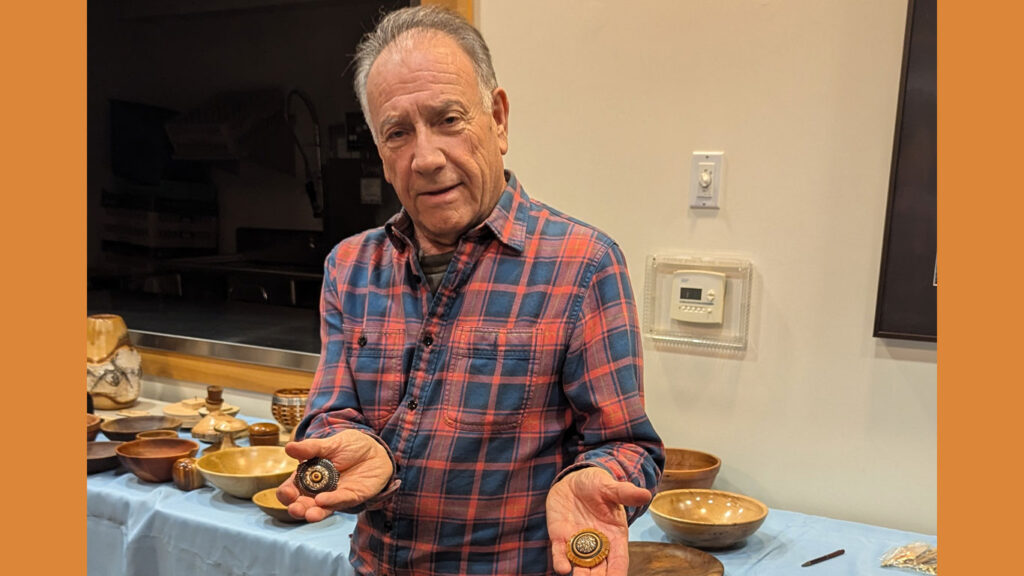
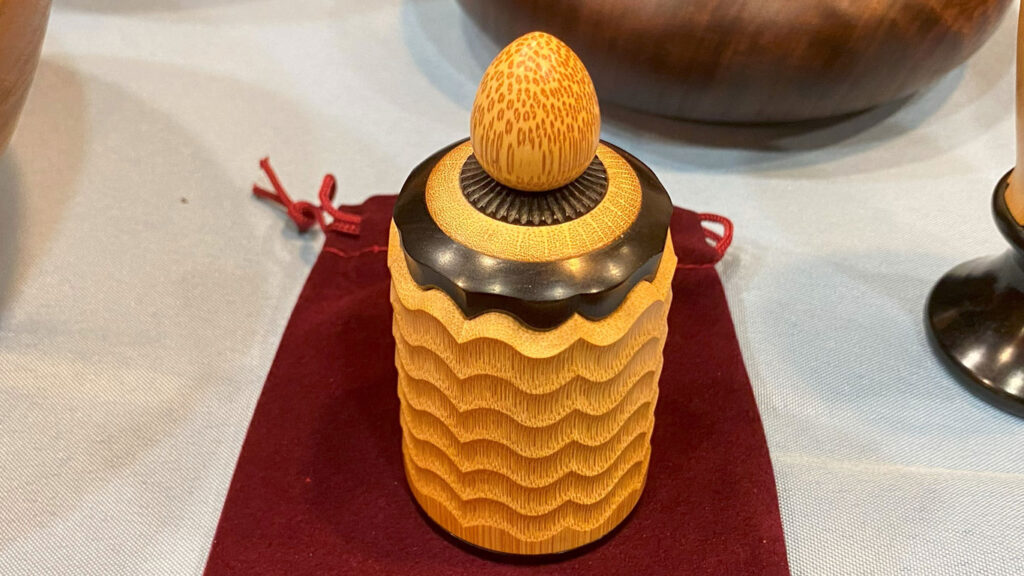
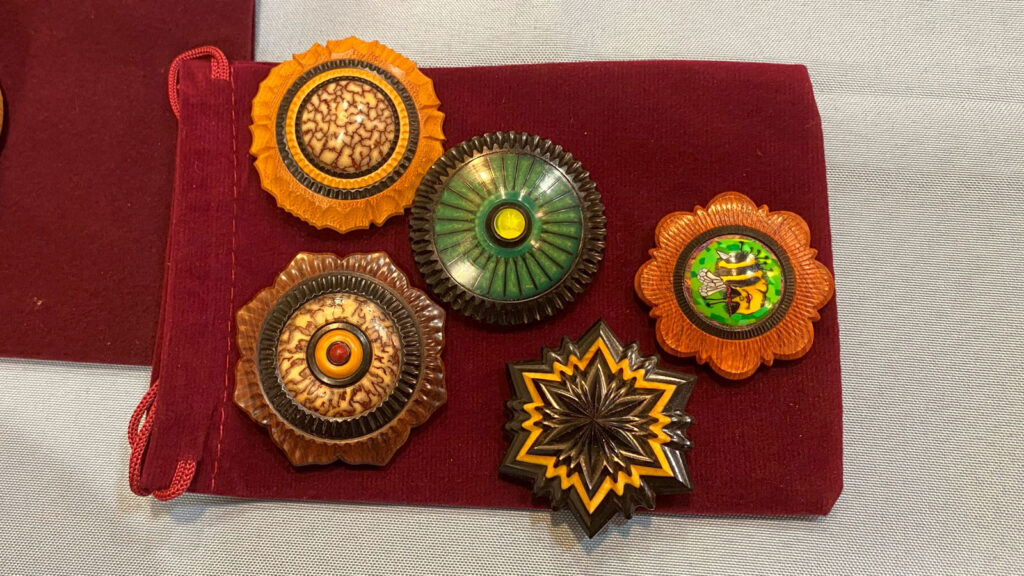
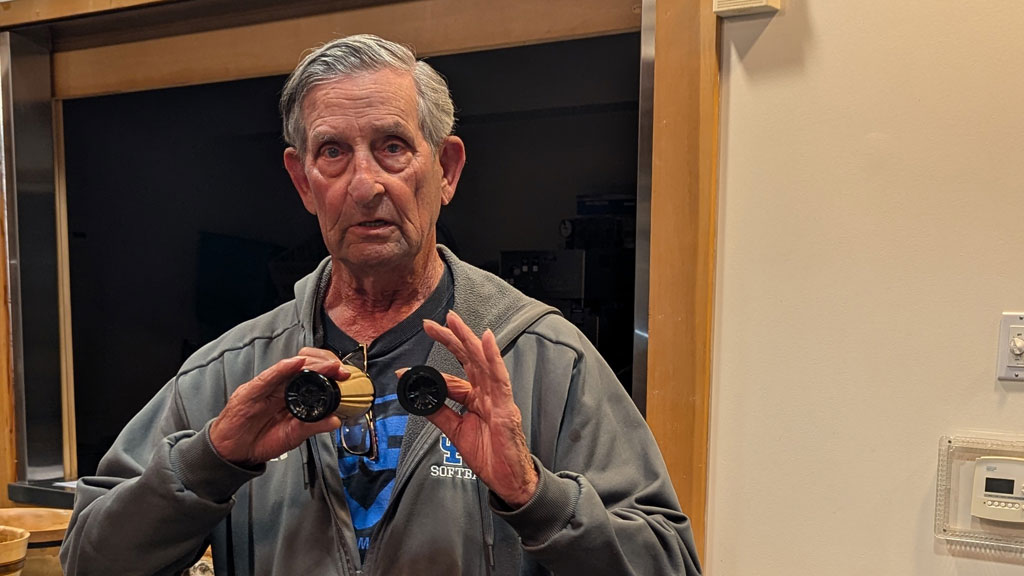
Dale Bassman made a vase using his Rose engine lathe using African blackwood, American holly and tagua nut. The top of the vase is shaped like the petals of a flower opening.
Tom Gaston showed two large Silver Maple bowls with dyed banding. He also brought a Liquidambar bowl and an ash vase with an asymmetrical rim.
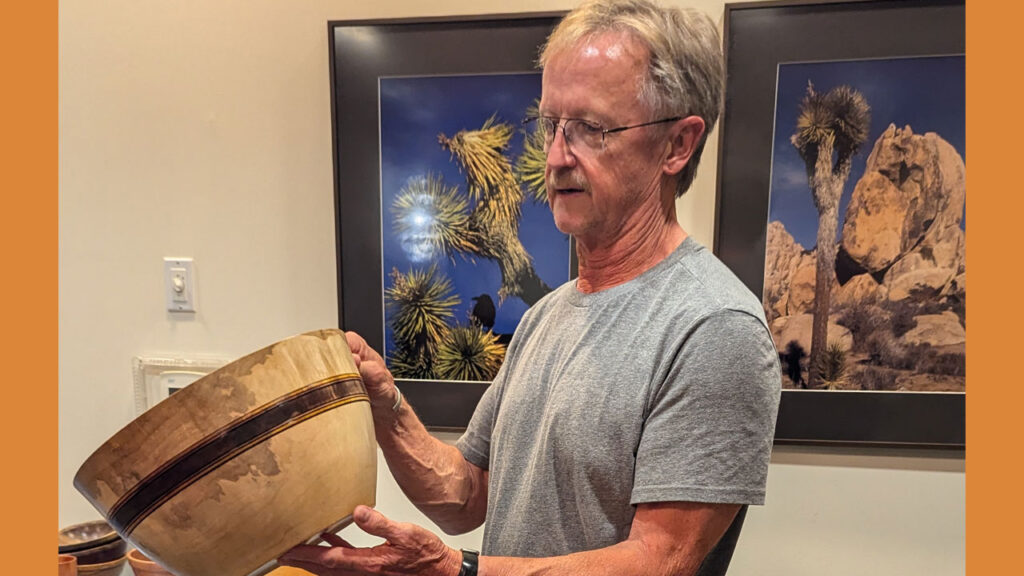
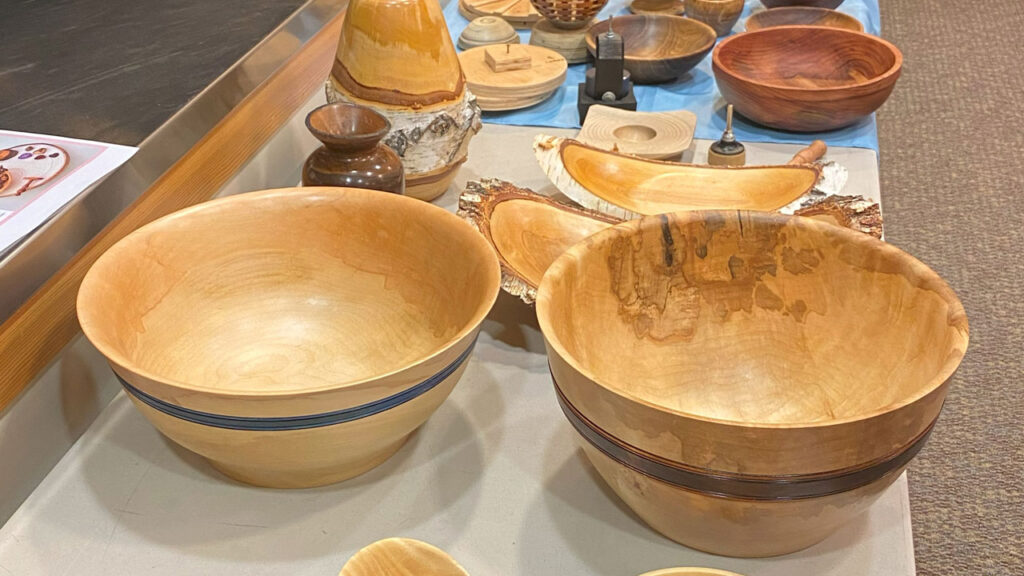
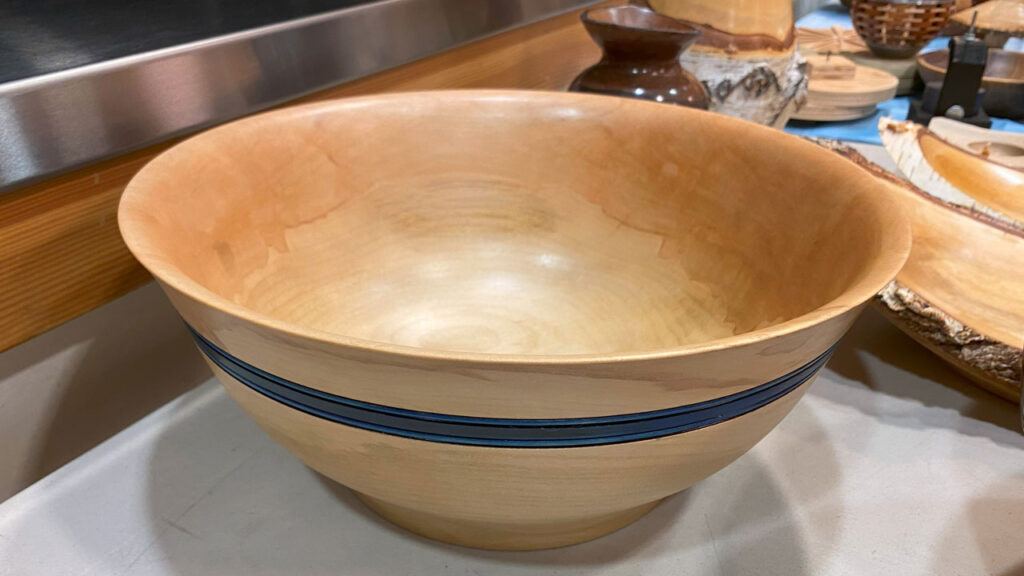
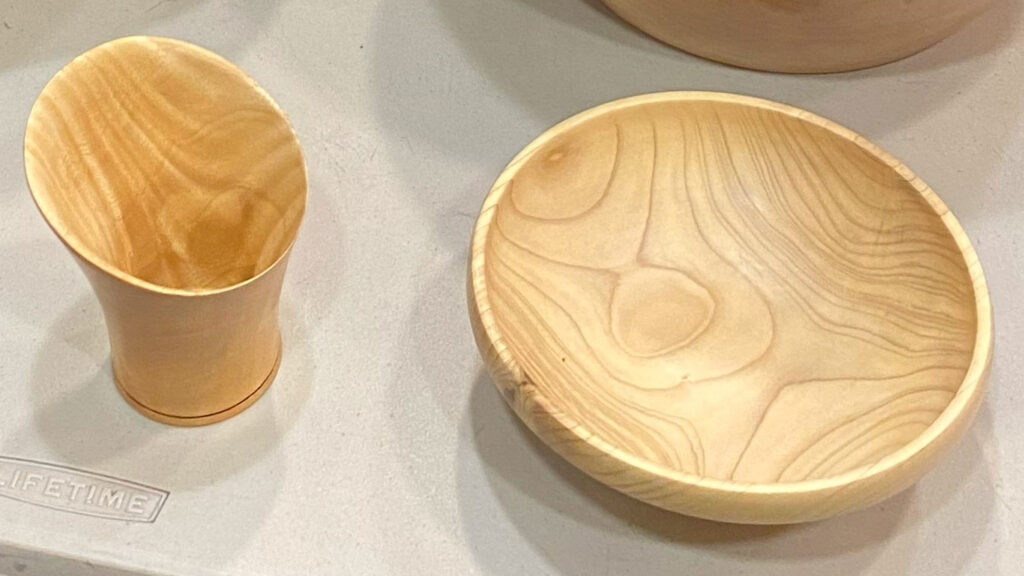
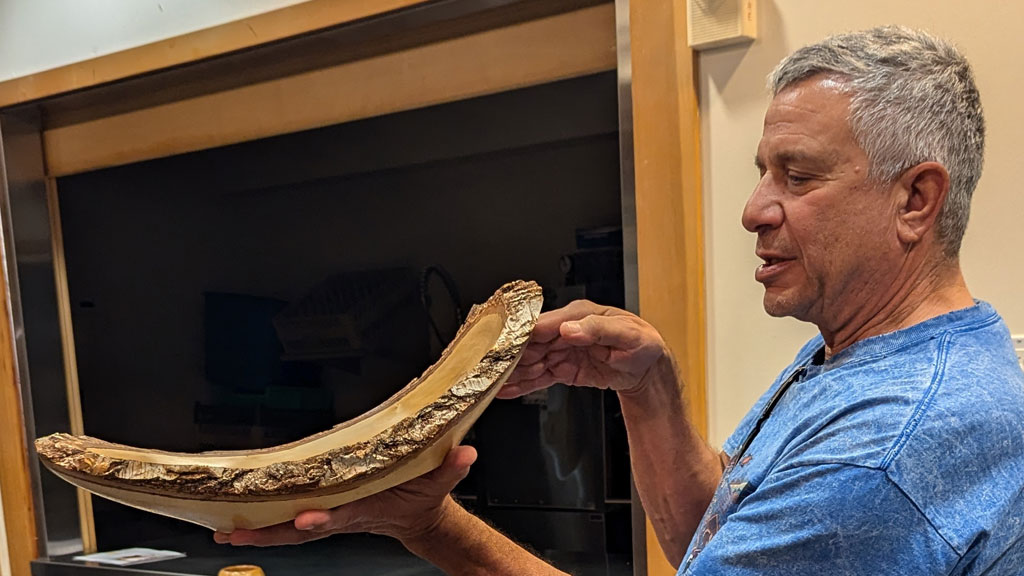
Bob Bley made a walnut vase. He showed a pair of natural edge birch platters. He used filler to help hold in the bark, sealed them with shellac, then applied wipe-on poly. Also from birch, he made an end grain hollow form vase with the bark still exposed on portions of the exterior. He used Pentacryl in the bottom to stabilize the pith. To waterproof the interior, he used Clear Coat epoxy from System Three. He applied shellac to seal the exterior.
Joe Martinka followed Eric Lofstrom’s advice and made a 1/8” burnisher from a solid carbide tile cutting router bit. Only the shank of the bit is used, the “business end” is buried in the burnisher’s handle. To achieve a long-lasting cutting burr on his scrapers, he uses a diamond hone to take off the burr from the grinder and then uses the burnisher to create a better-quality burr on the tool.
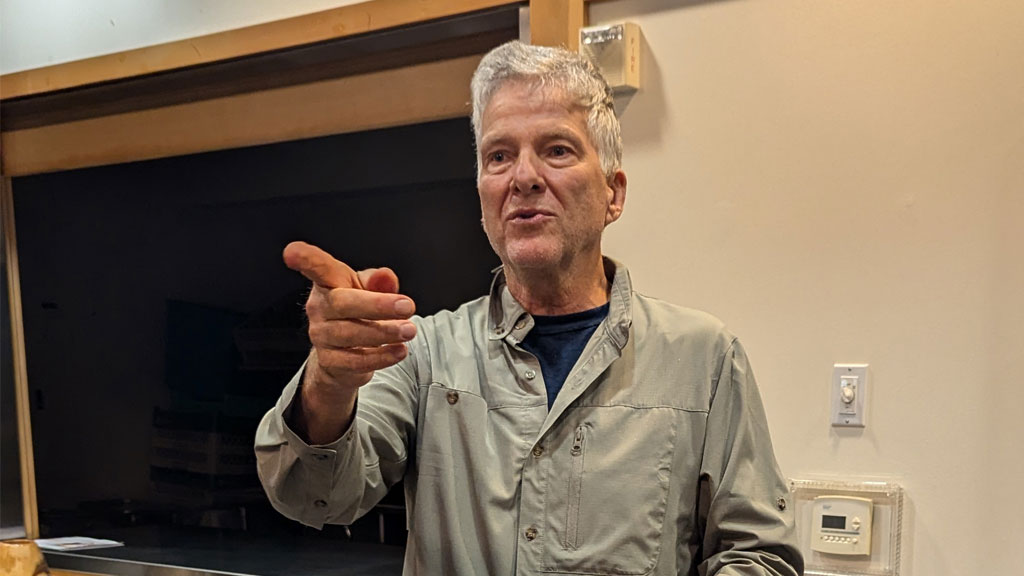
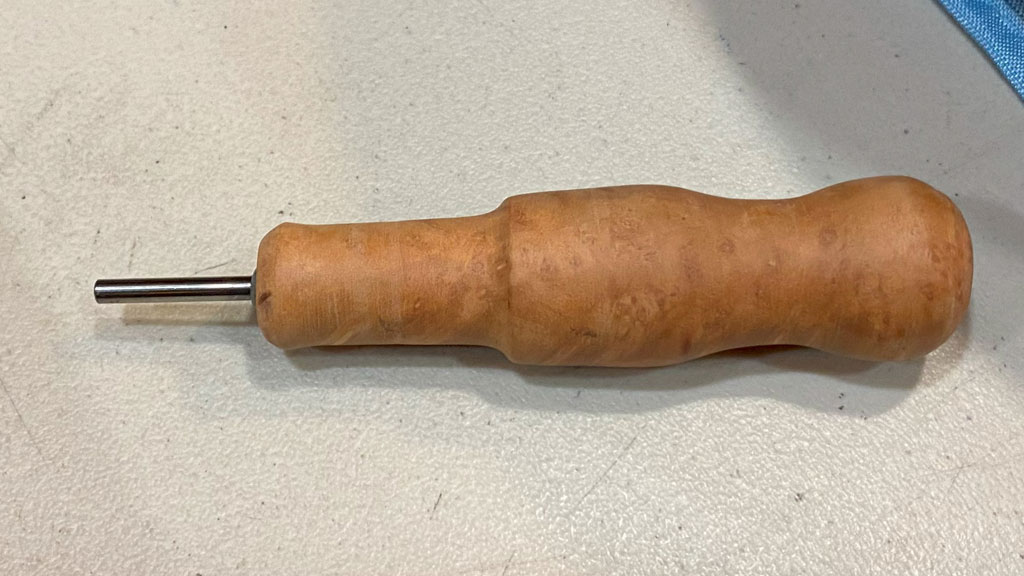
Dean Caudle made a box from his neighbor’s red bark eucalyptus with a camphor top. He also made a red bark eucalyptus goblet.
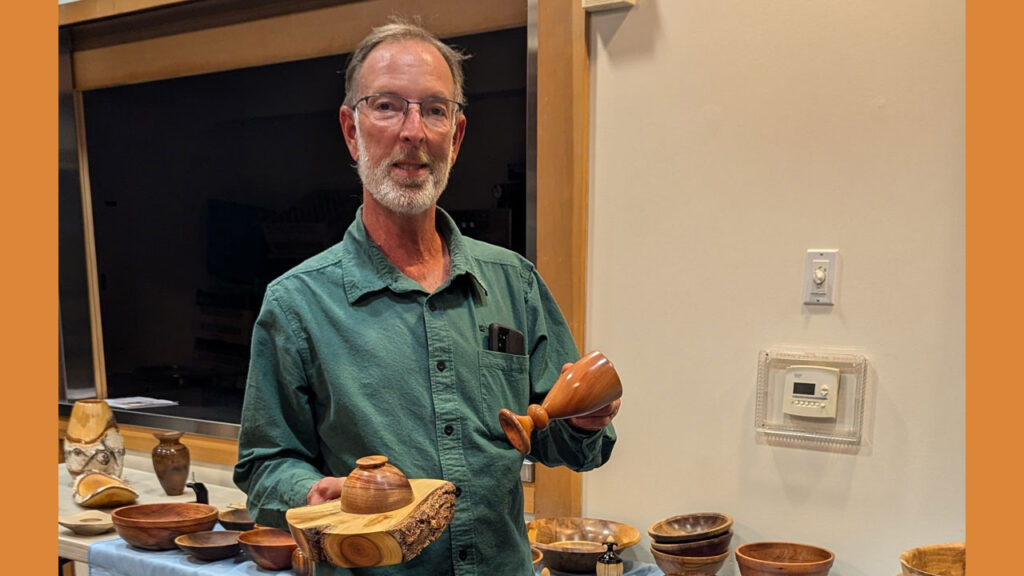
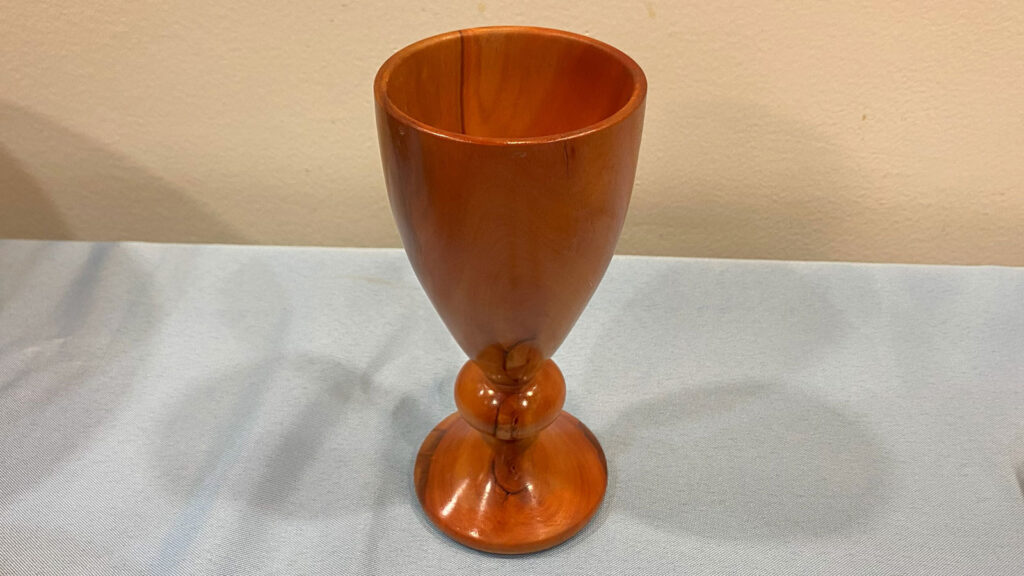
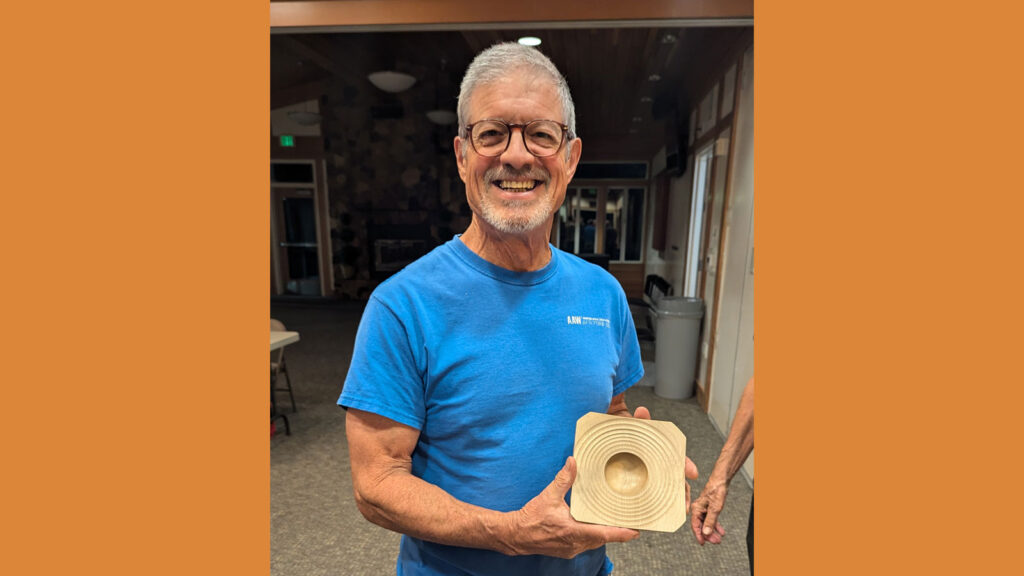
Jerry Galli made a ripple bowl (a la Eric Lofstrom) from bay laurel. He used a ½” bowl gouge fixed to his hip to create the radiating ripples.
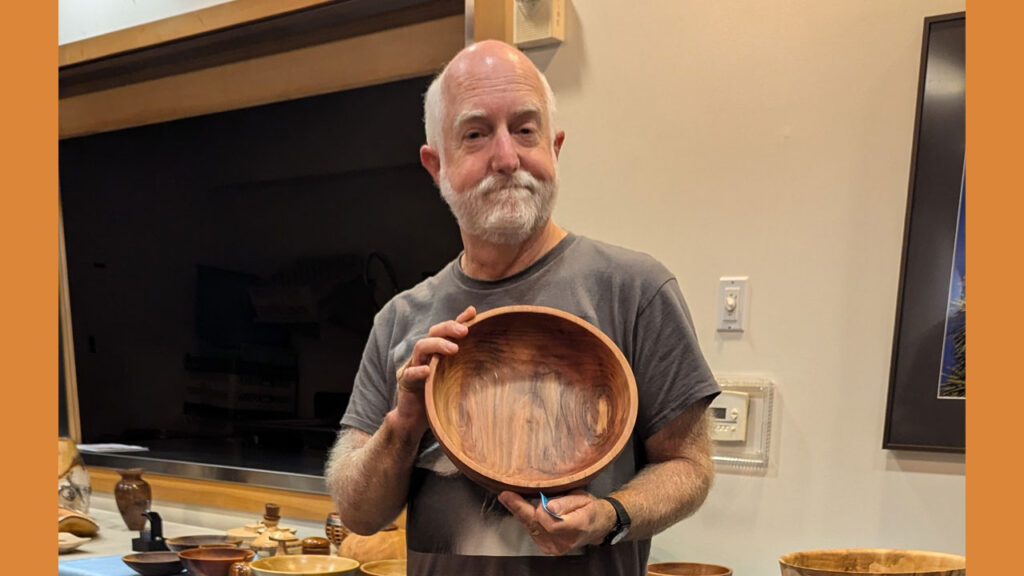
Vic Mitnick made a redwood bowl from a Stanford tree. He finished it with walnut oil, but it remained tacky for weeks.
Kelly Smith, as always, has been busy turning and showed a number of different creations, including: an offset mushroom; a lidded box; a pumpkin from Half Moon Bay cypress with an acacia stem; an apple from Portola Valley applewood; some bowls made from Tulip poplar given to him by a customer in Volcano; a box made from pear finished with CA and poly; a locustwood mushroom; a madrone bowl; a turned betel nut; and boxes from old bleacher seats. He noted that the pumpkin’s acacia stem was particularly difficult to carve. To create his pumpkins, he uses his lathe’s indexing system to make the lines and then carves the grooves, starting with a small rasp, then a larger rasp, then a file, then 100 grit sandpaper.
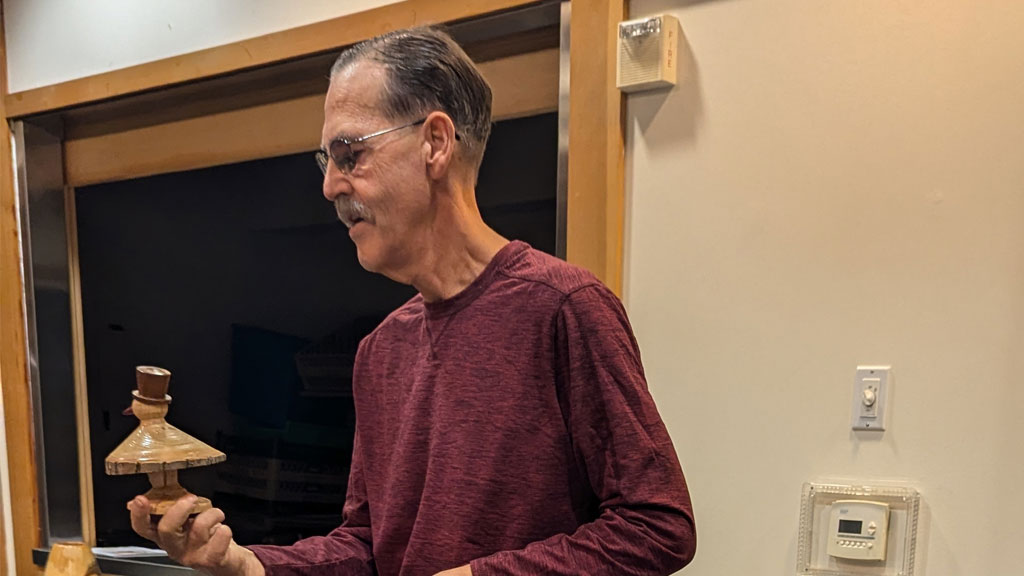
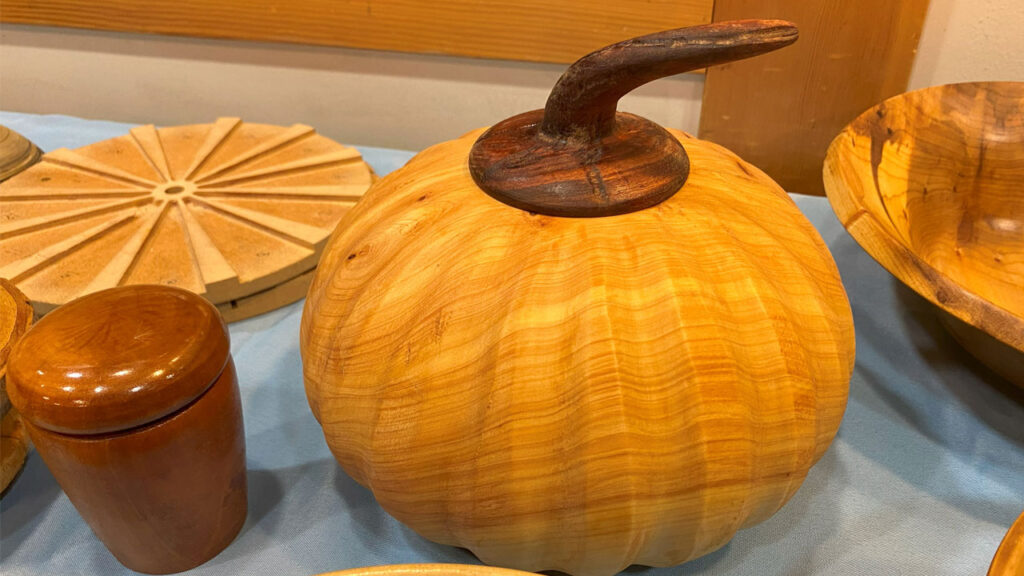
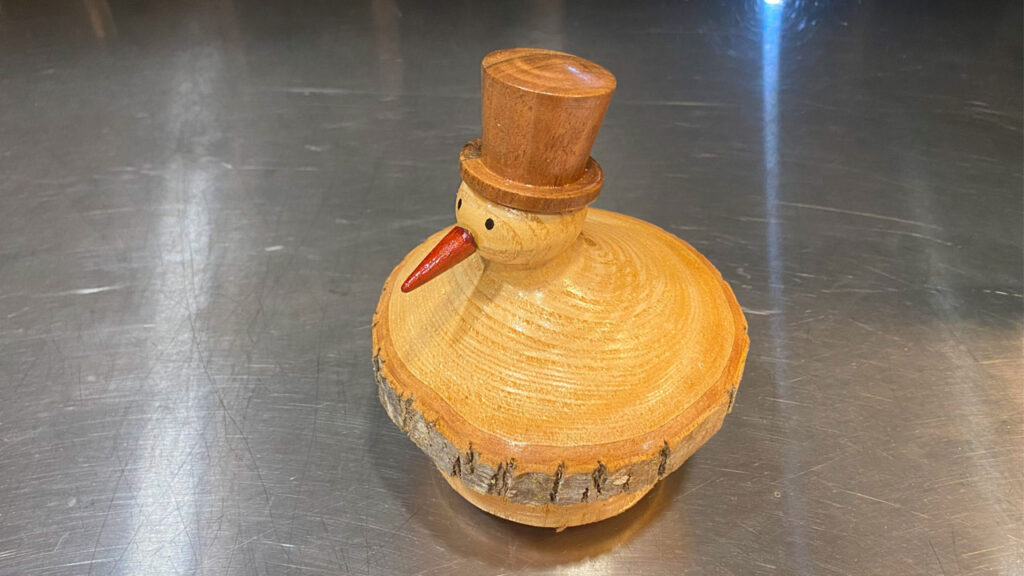
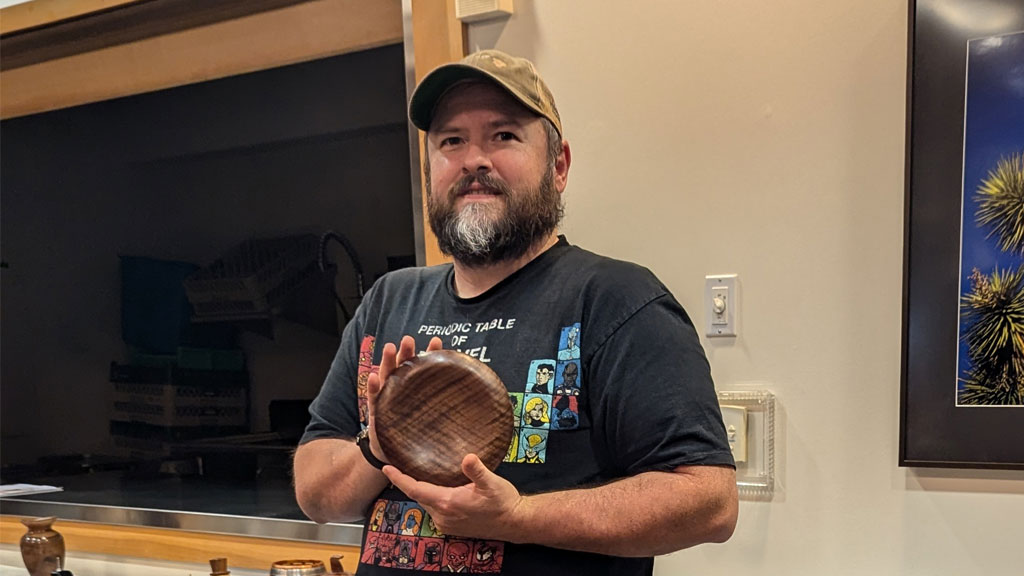
Nate Segraves made a pillow from curly black walnut, finished with bee’s wax and mineral oil. Bird and Branch Turnery Co. in the UK is credited with the shape.
Visit Nate’s Instagram.
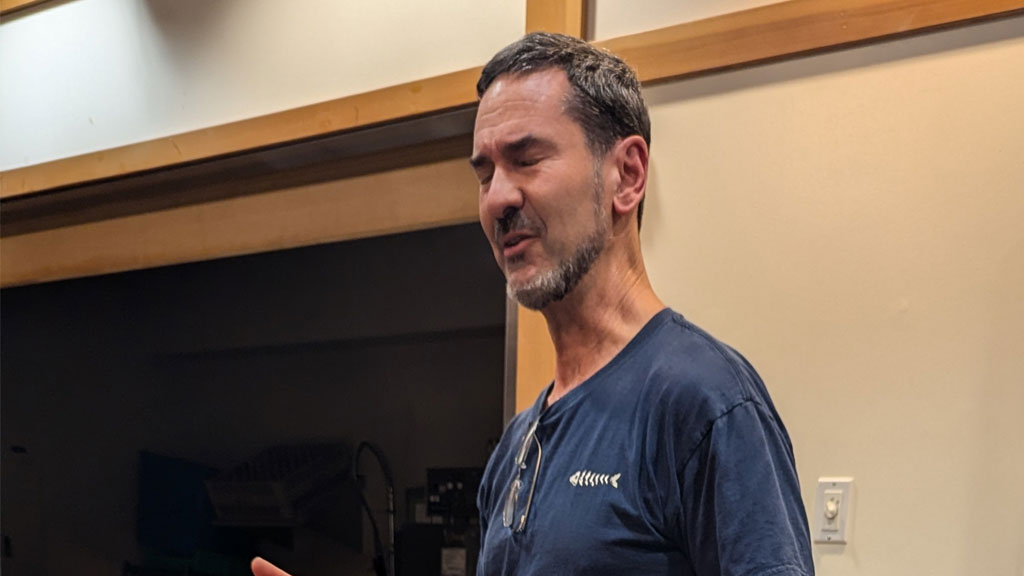
Chip Krauskopf emulated Eric Lofstrom’s custom gauges for setting up the grinder platform angle. Chip’s gauges were designed in Fusion 360 and cut/engraved with a laser cutter.
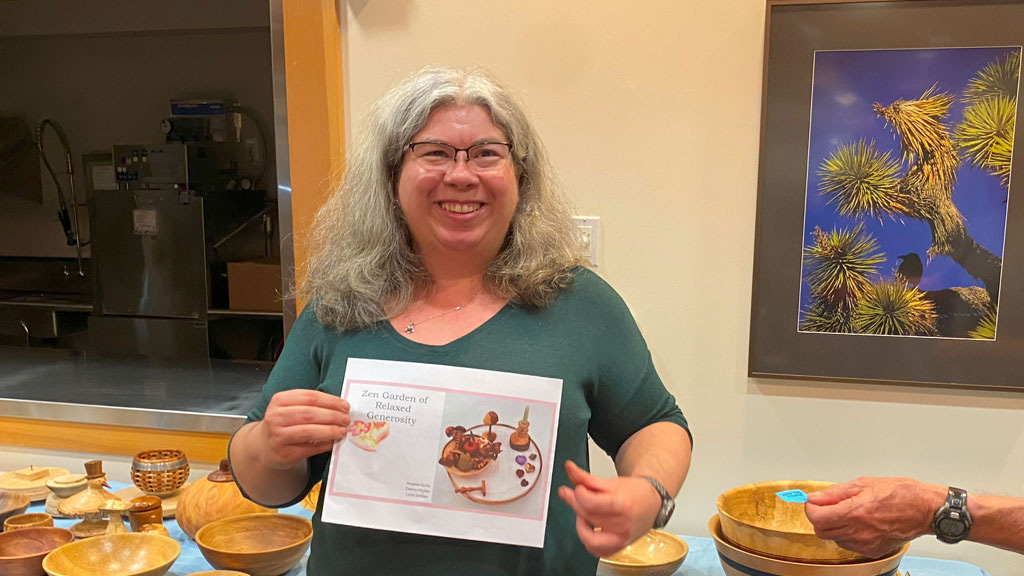
Angela Gunn showed a photo of the finished “Zen Garden of Relaxed Generosity” she created, along with two other turners, as part of the AAW 2024 Virtual Women In Turning Exchange. The piece features a lazy susan with a rake and sand and a collection of objects that reflect their group’s assigned phrase. On November 2, there will be an online presentation of all of the team creations from this year’s event.
Participation Prizes
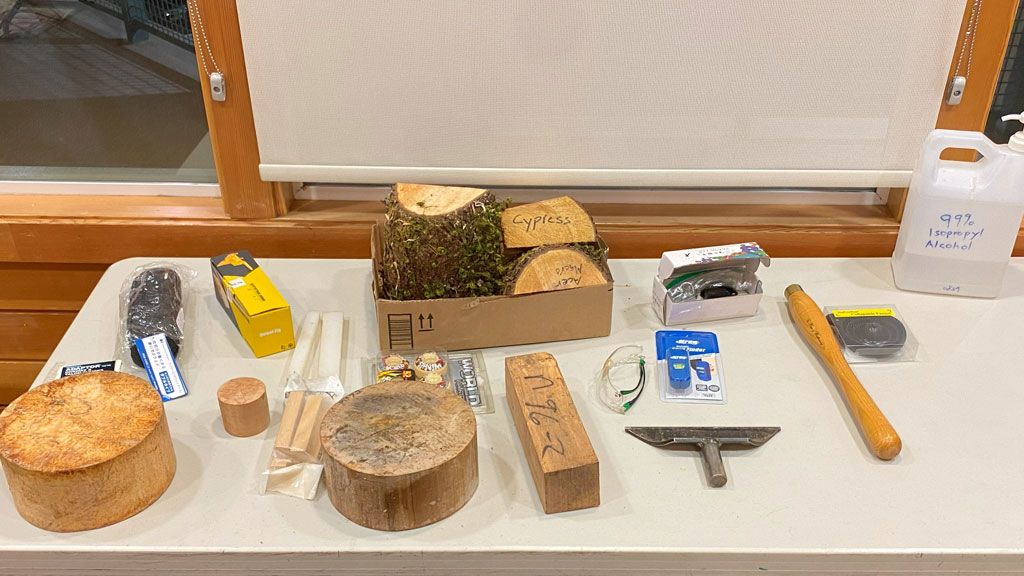
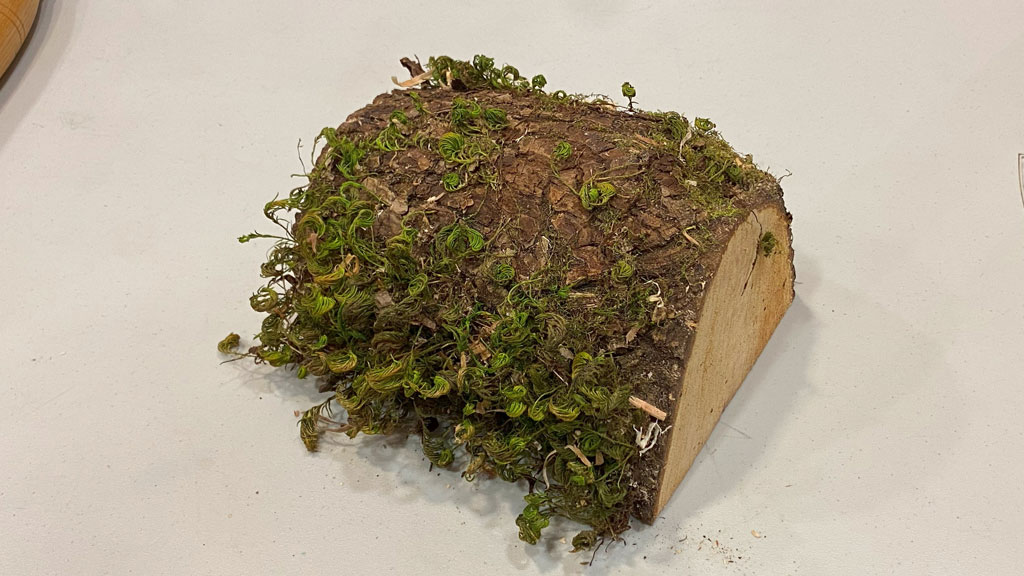
“As the Wood Turns” by David Vannier
One of my bosses said there are expensive lesson and cheap lessons in life. Expensive lessons are things you learn the hard way. Cheap lessons are things you learn from others expensive lessons. Take this as a cheap lesson.
I’ve been fortunate to not have any lung issues since I had Covid in Jan 2020. The pneumonia vaccine has really worked for me. I got lazy. I got a small piece of birch that was wrapped up in plastic before i took off for class. When i took off the plastic, i noticed some spalting had started. The wood was till sound, and it looked like a good piece to try more of the class work. Since i wouldn’t spend more than 30 minutes or so turning, i just put on my safety glasses and turned away. Very little sanding.
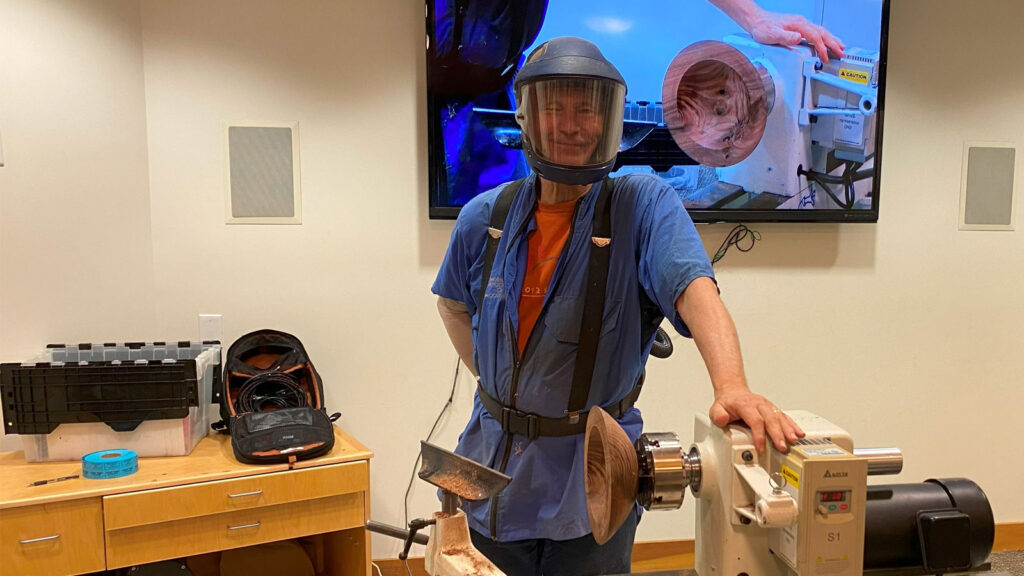
Then off to the wood burning. Rolled the station outside, turn on the fan, and away we go. Got it ready to paint, and quit for the day. Next day, full on asthma attack. Haven’t had an attack for at least 10 years. Sore throat, daring, and coughing stuff up. Ugh. 3 days later, I’m starting to feel like a human again. So was it the smoke? Well one of our professional turners has given up turning and moved to ceramics due to smoke issues. Was it the spalting spore? Was it a combination of the two? I thought the fan was good enough for the wood burning, but I’ve been doing some serious burning for several days. I know the spores can be bad, but thought I’d be ok. Moral is, no more burning or turning without the respirator! Learn from my mistake, save your lungs.
Woodturners Newsletter Editing Notes
WBW members, if you have a personal website and would like it included in the President’s Challenge and Show & Tell sections of our Woodturning Newsletter, please let the newsletter editors know. Email us at info@westbaywoodturners.com.
WBW board members and committee chairs
President: Claude Godcharles
Vice President: Tom Gaston
Treasurer: Jon Bishop
Secretary: Laura Rhodes
Member at Large: Dean Caudle
Meeting Program Coordinator: Claude G acting
Visiting artist Coordinator: Dean Caudle acting
Anchor seal: Dennis Lillis
Craft Supply: Tina
Librarian: Kelly Smith
Audio Visual: Curtis Vose, Edgar Whipple
Website: Roman Chernikov
Woodturners Newsletter: Angela, Claude, David, Laura, and Roman

Leave a Reply